They say the brightest of the diamonds are those which…
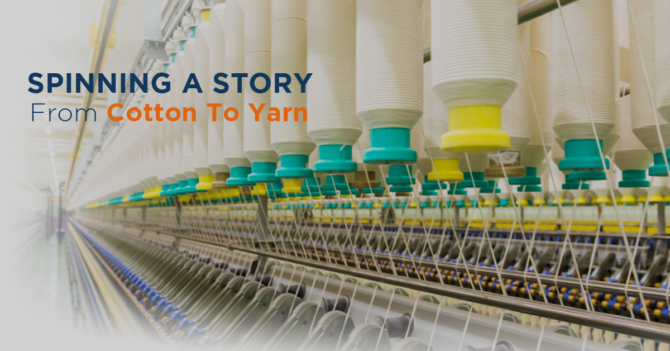
Spinning a Story, from Cotton to Yarn
Harvested cotton forms the raw material for the modern Spinning Jennies. From natural cotton to threads, the whole procedure is way more complicated than it is presumed. The dirt, blending ratio, even the length and thickness of fiber can alter the quality of the intended product. No doubt, automated systems are employed for acute-precision throughout the entire process in the spinning industry. Spinning can manufacturers have to account a lot on many such factors.
Unicleaning
The cotton bale gets rid of fiber-fragments and trash particles such as leaves, seeds, and sand. It is natural for cotton flowers to be filled with dust and dirt. The blowing machines compress the cotton fiber into sheets, turning them into- what is known as ‘lap’.
Lap preparation
Before the feed sliver passes through the comber, it is made even and parallel and is separated into individual strands. Huge metal rollers straighten the fiber. Later the slivers are aligned along a fixed axis in specially designed sliver cans so that they can be spun easily.
Sliver lap formation
A series of sliver cans placed in a row supply slivers that are intertwined loosely. The web thus formed, is rolled up to form the ‘sliver lap’. The quality of yarns is determined as the cotton is blended with other kinds of natural and synthetic fibers. The sliver is taken for further processing in sliver cans.
Combing
Multiple strands of slivers are combed to obtain long sliver yarns of uniform length. Finer cotton is combed twice.
Drawing
By the end of carding and combing process, the slivers have already elongated six to eight times their original length. After length, it’s time for thickness adjustment. All slivers are transformed into strings of uniform thickness and are stored in draw frame sliver cans.
Roving
The sliver is still not ready for spinning and hence passes through the auto-leveling machine where they are further elongated. Scanning rollers use electronic signals to control the thickness of the slivers.
The final stage
The finished thread is winded on bobbins of different shape, size, and color.
Now, just take some moments to imagine the amount of accuracy and hygiene required to handle all these different forms of cotton throughout the spinning process. Sliver cans of different shapes and sizes are used throughout the procedure. This way, we get the best fabrics that are directly transported to the textile industry for further processing.
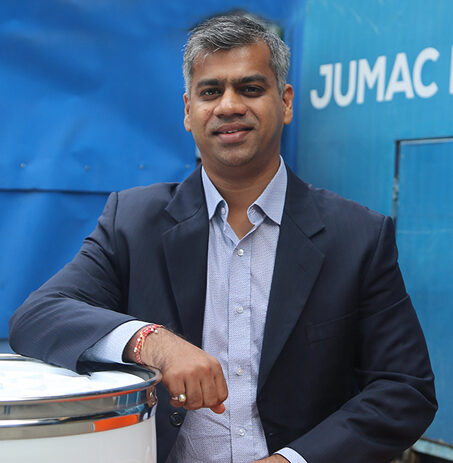
Passionate about transforming the industrial sector of textile and spinning industry with innovative solutions. Director at Jumac Manufacturing, leading spinning cans and accessories manufacturer and exporter from Kolkata, India.