Technology is changing the face of modern-day manufacturing facilities. The…
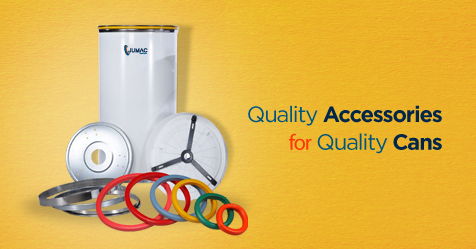
What Gives Shape To Your Sliver Can
Sliver cans are absolutely indispensable for the spinning industry. For all that quality fabrics processed by various industries, the sliver can have a major role to play. A close look at the spinning industry will leave you wondering about the diversity of the spinning cans– for they come in all size and colours. Even at a small-sized spinning mill, you will find hundreds of these cans that are used to transport, accumulate and collect different forms of slivers.
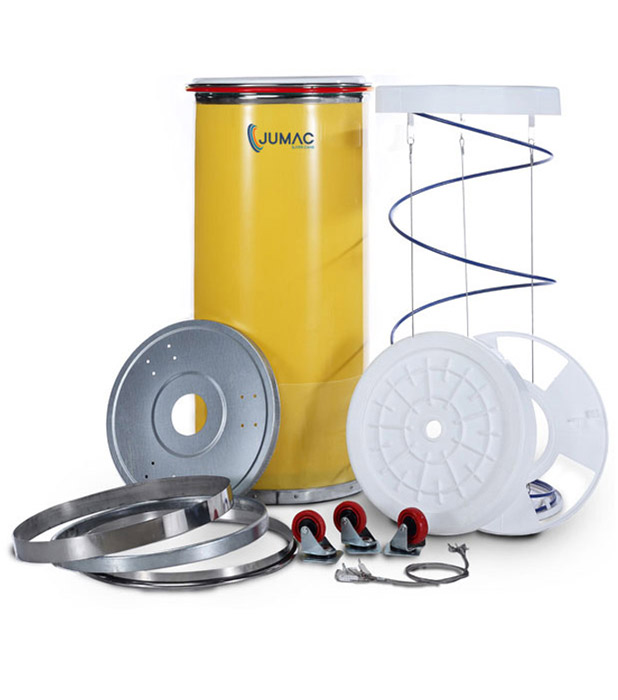
For this multifunctional component to deliver sliver in proper handling condition, the right kind of spares and accessories are necessary. The fact that the spares and accessories are responsible for proper functioning of the coiled springs makes them all the more essential.
Top and Bottom Covers
When spinning a huge amount of centrifugal force tends to affect the physical structure of the cans, making the cans prone to tilting and slipping, and ending up rupturing the sliver. This is why the top and bottom covers are added to sliver cans. Manufactured from Poly Propylene Copolymer (Moulded PPCP), the top and bottom covers prevent slipping of the cans from their respective bases.
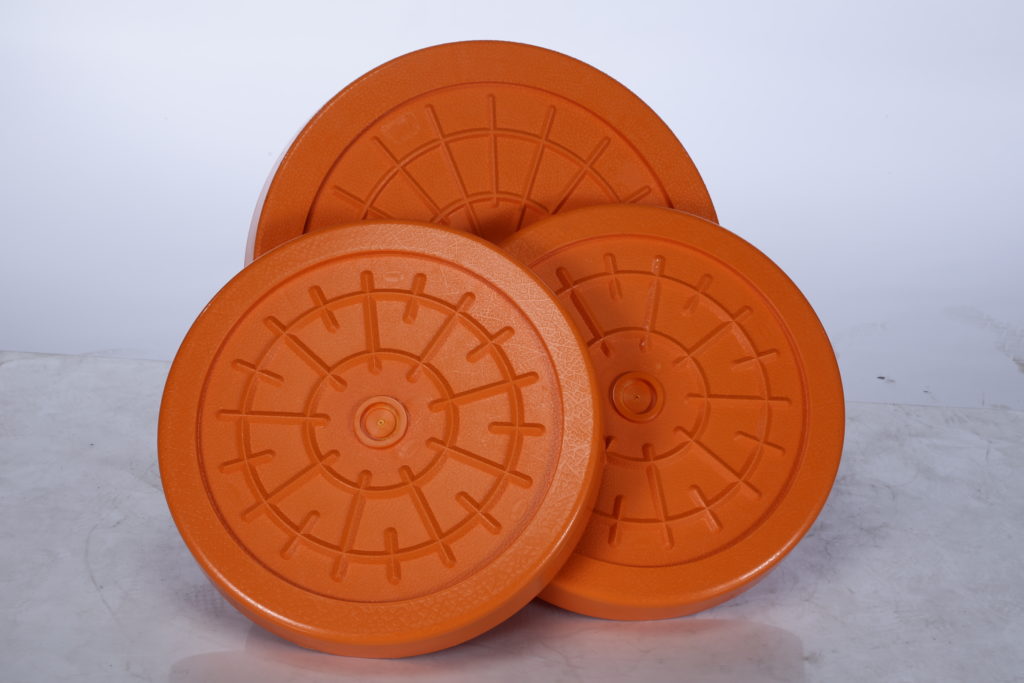
The surface grip of PPCP is strong enough to hold the cans in place. In a bid to improve durability and strength, Acrylonitrile Butadiene Styrene (ABS) is added to the top cover.
Top Rim and Band
At the brim of each sliver can, there is a rim made of SS (Stainless Steel) which is nowadays replaced by Galvanized Steel (GP),. The top rim upholds the shape of the sliver cans, preventing the cans from developing cracks and collapsing when rotating under high speed. It is not possible to reverse the sliver handling at any stage of yarn production.
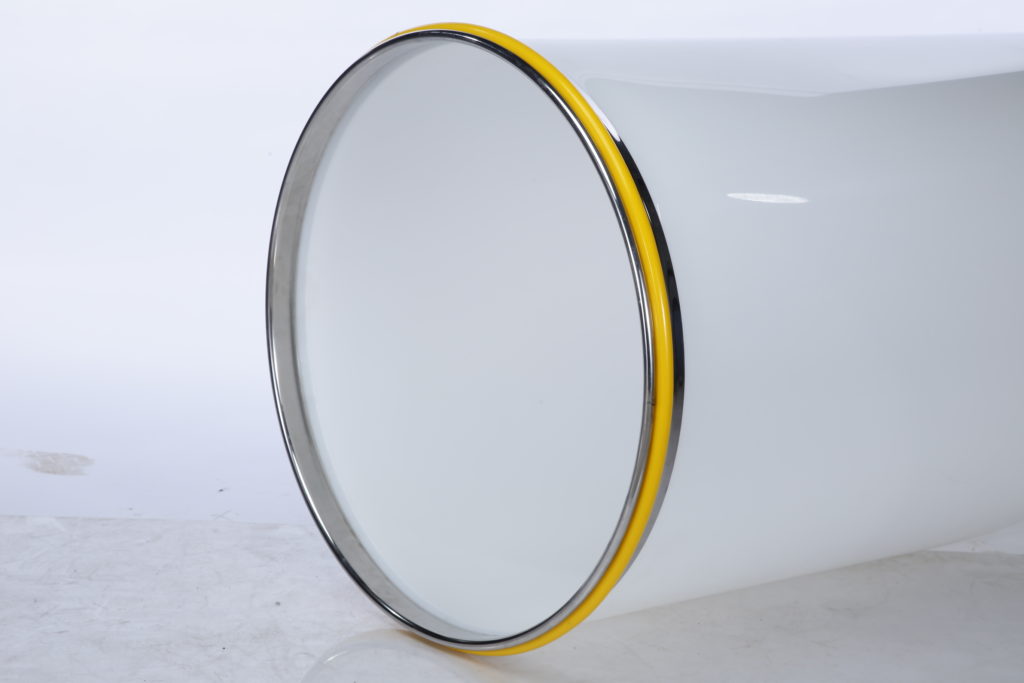
The backbone of the sliver cans- the springs, are also supported by the top rim and the band, which are fixed by swaging machines. They also safeguard the sliver from the pressure of the spring during rotations.
Bottom Rim and Plate
An additional support plate lies at the bottom of the sliver cans. These GP plates are obtained from heavy duty power press. Additional ribs and contours hold the balance of the cans. The bottom rim either has caster fittings or is connected to caster adapters. Along with the rims, the bottom plate increases the longevity of the sliver cans.
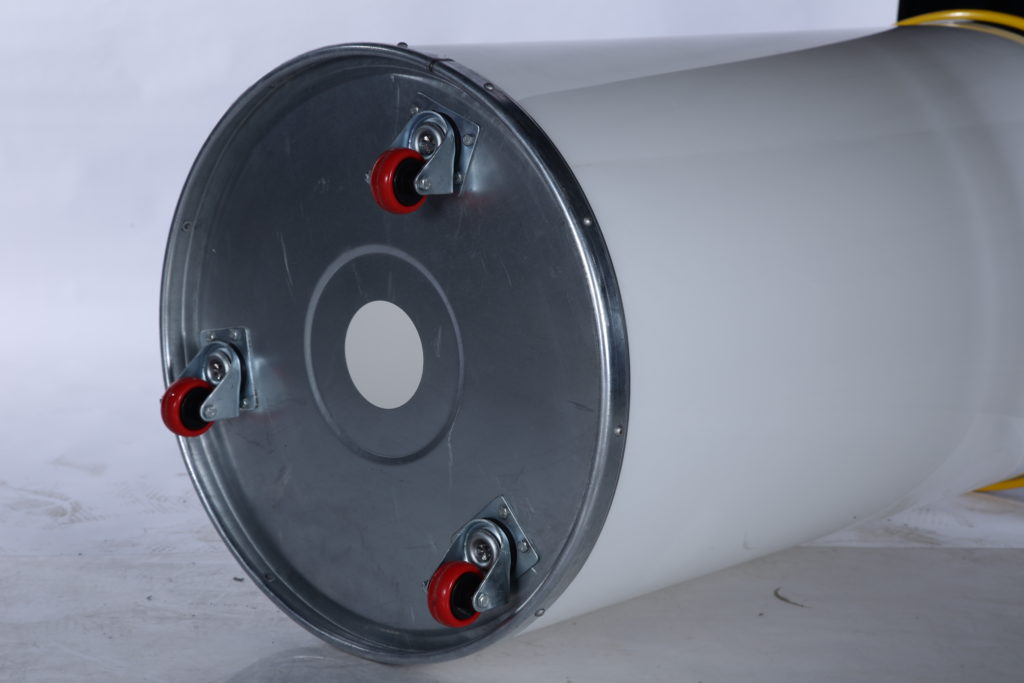
The bottom rim and the plate allow perfect adjustment to the toothed belts. Usually, the plate rotates in the direction of the can but sometimes it is engineered to rotate in opposite direction also.
Identification Bands
To distinguish slivers at different stages of yarn processing, identification bands are added to sliver cans. For instance, a set of combed slivers can be set apart from the ones that are aligned for the carding machine by their identification band. Normally, all HDPE cans of similar height, colour and diameter are indistinguishable. Different colours of PVC based identification bands at the topmost border of sliver can also provide an attractive façade to the cans.
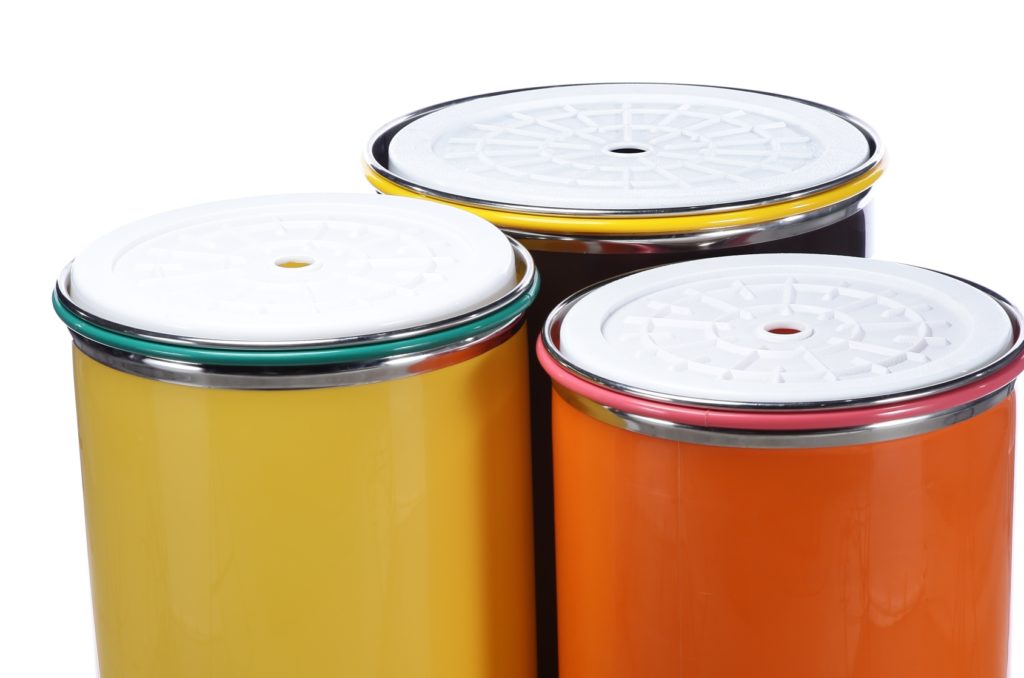
Not just colour bands, they a utility too. Besides being a medium for identification, the bands function as shock absorbers, making the cans strong and robust. PVC is a highly stable material and gives adequate rigidity to the sliver cans during bumping or other handling conditions. It also makes differentiating sliver counts during all stages of production.
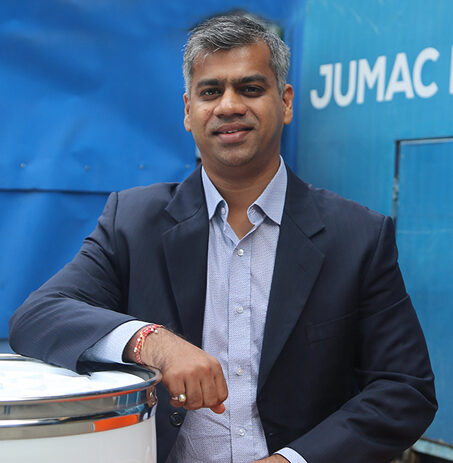
Passionate about transforming the industrial sector of textile and spinning industry with innovative solutions. Director at Jumac Manufacturing, leading spinning cans and accessories manufacturer and exporter from Kolkata, India.