The winds of change are well and truly blowing, as…
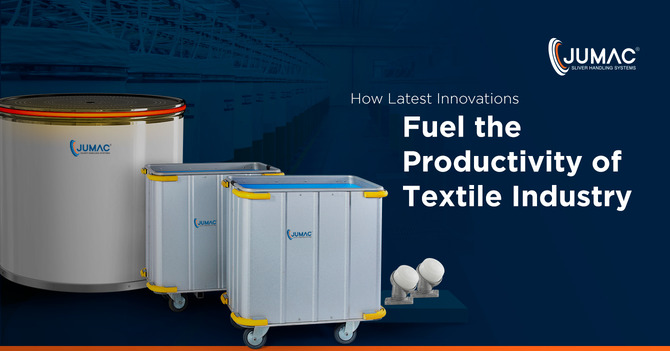
How Are The Latest Innovations Fueling The Productivity Of The Textile Industry?
With nearly 5% share in the worldwide textile & apparel industry, India is well and truly a major global player from this sector. Indeed, the domestic textile sector is making rapid strides – with the CAGR for this industry expected to hover around the 10% mark till 2025-2026 (the value of the Indian textile & apparel sector will be ~$190 billion by that time). Exports of Indian textiles are also increasing at exponential rates. Technology advancements and innovation are playing key roles in the proliferation of the industry – with textile machinery manufacturers (OEMs) and suppliers of spinning cans constantly upgrading to the latest technologies, to deliver value to customers (i.e., mills). In here, we will focus on how the innovations are optimising the productivity and shaping the future of the Indian textile sector:
3D Printing is Becoming More Mainstream
In the increasingly competitive world of textile-making, manufacturers need to establish their USPs and operational capabilities to stay ahead of the competition. 3D printing methods are helping in a big way on this count. With custom 3D printing, textile designers are being able to come up with apparels of different (and relatively complicated) shapes. As a result, the final product is becoming more appealing, customised and also better from the sustainability count.
By implementing 3D printing methods, fashion textile manufacturers can also make their day-to-day operations smarter, more agile and more productive. With just-in-time (JIT) production emerging as a very real possibility, the issue of overproduction, and resultant wastage, are getting minimised. In the textile and apparel sector, waste-management is a major challenge – and 3D printing techniques can do away with these problems effectively.
The Rise & Rise of IIoT and Automation
Traditionally, the textile sector has been a highly labour-intensive one. In the relatively larger mills in particular, maintaining efficiency and productivity levels – while managing practically everything manually – can be problematic (if at all possible). For instance, checking the level of slivers in the hundreds of spinning cans manually is a hugely time-consuming and exhausting task. To make things smarter, with centralised visibility and control, mill-owners as well as spinning can manufacturers are leaning on data-driven automation, AI and Industrial Internet of Things (IIoT).
Must Read : IIoT Applications for Textile Industry- Jumac Takes an Edge
Through adoption of automation, textile manufacturers have plenty of opportunities to rule out manual errors & uncertainties from their operational processes. That, in turn, would eliminate the chances of production slowdowns. The domain of textile-making has become more & more ‘connected’ – with authorised personnel being able to monitor spinning can health and status of sliver handling processes with ease. Predictive maintenance has also become possible.
New Supply Chain Technologies are Emerging
The demand for competitively priced apparel is increasing at a rapid clip globally. To meet these burgeoning demand levels, textile manufacturers are adopting new supply chain methods that ensure a circular, fast-moving economy and closed-loop product handling environments. These tech-based supply strategies are proving to be instrumental in eliminating delays in the products reaching the buyer. The focus is squarely on establishing tech-powered supply chains that ensure greater traceability, quality-assurance, and full accountability.
With textile supply chains becoming increasingly streamlined, operations are becoming more cost-efficient as well. Things like robotic textile handling, automated folding, and usage of renewable power sources are growing common too. Thanks to computer vision and high-end machine learning (ML) technologies, the quality of the textile products are being optimised. Digital advancements are right at the heart of modern textile manufacturing.
The Best of Mobile Technology to Ease Service Concerns
In production processes, uncertainties are never a good thing. This holds true for the textile manufacturing sector as well. Earlier, there was a lack of accurate information regarding machinery specifications/performance, ordering & delivery of spinning cans, and other related details. This, in many cases, resulted in mills not being able to operate at full capacity and/or being bugged with quality issues.
Mobile technology, in the form of smartphone applications, have emerged as effective tools to counter these problems. There are user-friendly, information-rich apps (the Jumac Smart Cans app is a classic example) that allow mill-managers to check out can details, order sliver cans and track their orders at all times. In addition, staying on top of all the latest news and updates from the Indian textile industry – while on the move – has become feasible. With updated information available right at the fingertips, uncertainties are being eliminated.
The Digital Journeys of Textile Manufacturers Have Kick-started
Like all other business sectors, the domestic textile industry was also hit hard by the global pandemic. However, this period also threw up opportunities for manufacturers & suppliers to re-examine how they can take their business forward. In particular, the virtues of using digital methods – in the form of virtual models and virtual shows – towards creating more robust business models became apparent. In the post-pandemic world, these virtual technologies will continue to gain in momentum.
In addition to virtual textile sector events, manufacturers are also embracing AR/VR to push productivity levels, and to power up their marketing efforts. In addition to being efficient and easily manageable, these digital methods have lowered carbon footprints significantly – ensuring greater sustainability. Also, breakthrough innovations like temperature-sensitive clothing (as displayed by Ralph Lauren) are gradually coming into focus.
The Compatibility Factor
Boosting textile and yarn productivity levels is all about optimising each and every stage of sliver spinning. For this, the top OEMs – from Rieter and Trutzschler, to LMW, Marzoli, Saurer and others – are regularly coming up with newer, more customised spinning machines for carding, combing, draw framing & more. Seamless compatibility between OEMs machines and sliver cans ensure better yarn quality, higher productivity and minimal downtimes. While procuring and setting up these modernised machinery is simple enough, the challenge lies in making sure that the spinning cans used in them are compatible with the machines.
In order to avoid problems on this count (that can lead to extended production downtimes), any leading spinning can manufacturer in India is coming up with sliver cans that are fully compatible with all the leading spinning machinery OEMs (and their latest models). As a result, operational efficiency on the mill floors is not being affected in any way. The interruption-free manufacturing is pulling up overall productivity and profitability considerably.
The Move Towards Sustainable Packaging
The textile industry is, by nature, ‘waste-heavy’. A recent report showed that the sector generates nearly 2.2 billion tonnes of waste annually. A lot of the new innovations – apart from enhancing productivity & efficiency – will also reduce the ecological impact of textile manufacturing operations. Right from the growth in popularity of biodegradable raw materials, to awareness about the need for sustainable packaging – the innovations are indeed making textile & yarn manufacturing ‘cleaner’.
In particular, packaging options that are non-biodegradable cannot be disposed of or recycled. This poses an additional burden on the environment. Going forward though, manufacturers will focus more on adopting innovative, biodegradable packaging solutions – to keep things sustainable. Fibre wastes will be eliminated to the maximum extent possible too, ensuring greater productivity.
While the role of technology has been immense in the growth of the textile & yarn-making sector, it has not been the sole factor. Over the last half a decade or so, the industry has received healthy investments. For instance, between 2000 and 2022, the volume of FDI (foreign direct investment) coming into this sector has been well in excess of $3.85 billion. The favourable government schemes (the PLI scheme is a classic example) are also driving things forward. Together, spinning can manufacturer companies, OEMs and spinning mills are coming together to take this industry forward and consolidate India’s position as a powerhouse in textile-making.
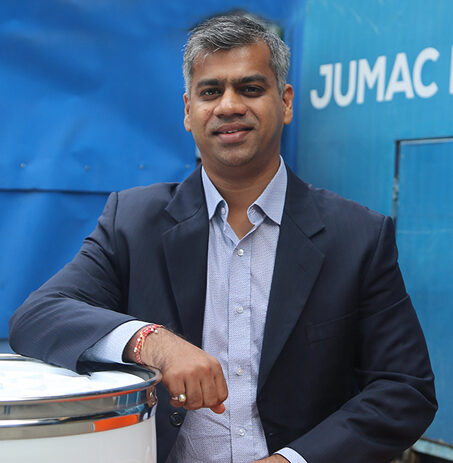
Passionate about transforming the industrial sector of textile and spinning industry with innovative solutions. Director at Jumac Manufacturing, leading spinning cans and accessories manufacturer and exporter from Kolkata, India.