The sliver cans manufactured for the spinning industry are used…
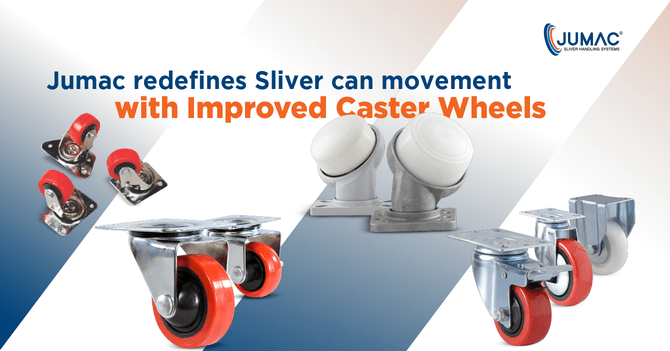
Jumac Redefines Sliver Can Movement With Improved Caster Wheels
On mill floors, the way in which loaded spinning cans are moved (either manually or with the help of automation) has a direct impact on the overall sliver handling quality. Given the generally rough/bumpy nature of floor surfaces, this becomes all the more important. When there are problems in sliver movements in cans, the entire process is disrupted, there are delays, and operational efficiency levels go down.
As a globally recognised sliver can manufacturer company, Jumac offers different categories of quality-optimised, highly-durable caster wheels – to ensure smoother, better can movements on mill floors. Over here, we will highlight how we are constantly redefining sliver can mobility with our precision-designed casters:
What Advantages do our Caster Wheels Deliver?
Irrespective of whether the casters are custom-fitted to the spinning cans, or there are fitting options in the galvanised rims/bottom plates, they ensure uniformly smooth sliver mobility on the mill floors. During the movement of cans from one place to another, risks of tipping over – which can cause irreversible sliver damages – are eliminated as well (this is extremely important for loaded cans). All cans manufactured by us are fitted with highly durable caster wheels that make sure there are no problems during the can loading and/or unloading stages. Our casters ensure that spinning can performance is optimized at all stages of yarn production.
Features & Properties of our Casters
When it comes to enhancing the operational efficiency of sliver can usage at mills, the role of our precision-engineered caster wheels is paramount. By ensuring faster, smoother sliver movements, the casters go a long way in ruling out time-wastage and ensuring that there are no delays in the overall process.
As a leading sliver can manufacturer in India, we make sure that our caster wheels have top-notch mechanical features and capabilities. The high mechanical strength of the wheel material, together with strong abrasion-resistance and impact-resistance, do away with chances of excessive wear & tear – even after prolonged periods of usage. This, in turn, boosts the overall longevity, and frequent replacements & repairs are not required. The minimal rolling resistance of our casters ensure easy mobility of the cans on mill floors. The excellent static load-bearing capacity of Jumac caster wheels is yet another advantage.
Types of Caster Wheels by Jumac
Based on the precise can movement requirement and diverse mill needs, we have different types of caster wheels in our portfolio. All varieties of casters are of assured quality, and deliver optimised mobility of sliver during all spinning stages (carding, combing, draw framing, roving, etc.).
Our Durable Series of casters has been manufactured in a manner to perfectly sync with the bottom plate holes. These caster wheels have diameters ranging from 78.5 mm to 85 mm – and come in various fixing shapes (apart from rectangular and square shapes, plates in the shape of trapeziums are also available).
The Pioneer Series of caster wheels by Jumac are available in two different size options – 3 inches and 2.5 inches. This range of casters rank high on the durability count, and are also instrumental for prompt and regularised sliver cleaning. The wheels have a gap from the holding frame.
At the India ITME 2022 event (8-13 December), we launched our latest caster wheel variety – Supremo Casters. These are aluminium alloy wheels that offer true fluff-free assurance to mill operators (thanks to their ‘Ever Clean’ feature). The Supremo Casters have been particularly designed for maintaining the cleanliness of mill floors at all times, and ensuring that there are no suction-related problems.
The Importance of Fluff and Dust-Free Assurance
When a spinning can is fitted with sub-standard casters, fluff-accumulation becomes a very real problem. As fluff and dust continues to collect on the can wheels, chances of the spinning cans getting jammed (thereby making sliver movements bumpy and non-uniform) go up considerably. That’s precisely why all our caster wheels have anti-fluff-accumulation properties. Sliver transportation on mill floors are refined, there are no risks of the cans tilting/falling, and the cans can be used for a long time.
Note: With minimal surface friction, our caster wheels do not leave any mark on the floors.
Trolley Casters by Jumac
In order to ensure smoother, better sliver transportation & bobbin storage, we have a diverse array of trolleys (perforated and non-perforated) in our portfolio. For these trolleys, we manufacture specialised trolley casters – with a load-bearing capacity of 500kgs (max). These caster wheels are available in 100mm to 200mm sizes, and make sure that there are no mobility challenges to hamper the steaming, auto-doffing, dyeing, and other related processes.
Best-In-Class Quality for Superior Longevity & Performance
To ensure that there are no problems bugging sliver can performance, we use the best-quality material to design our caster wheels. Nylon 6 and Polypropylene (PP) are typically used to make the wheels – and due care is taken to make sure that the wheels have the requisite capacity to support different sliver loads. As a result, the service life of our casters is invariably on the longer side.
Understanding Caster Wheel Fittings
Broadly speaking, the casters that are fitted with HDPE spinning cans are of two types. First, there are RIGID CASTERS that let the can move in a single direction (with stopper and fork fitted in). On the other hand, there are the much more popular SWIVEL CASTERS with 360° rotation – ensuring that the sliver can may easily move in any direction.
Note: As expert sliver handling solution providers, we make sure that the casters of the right size are always fitted to our spinning cans. There are minimal maintenance requirements – thereby delivering greater convenience to mill operators.
Nylon Wheels Vs PP/PPCP Wheels
While PP/PPCP casters are frequently used, they have their downsides. For instance, these wheels can get easily cracked when exposed to high temperatures (i.e., the wheel material can melt). PP/PPCP casters typically show more signs of wear & tear too. Our range of lightweight, chemical/abrasion-resistant nylon wheels can endure rough handling on the mill floors without any significant degradation. They are suited for movement on relatively uneven surfaces, and also lasts longer.
Ensuring a Smooth Move to a Stronger Sliver Handling Ecosystem
At Jumac, we constantly reiterate the importance of handling delicate sliver with care at mills. For this, we keep upgrading our portfolio with customised solutions that make sliver management better. The importance of ensuring smooth & seamless spinning can movements on the mill floors is paramount for maintaining the desired sliver quality parameters. Our series of caster wheels ensure precisely that.
With a keen eye for detail regarding every aspect of textile spinning and yarn handling, Jumac has been successful in consolidating its position as a leading sliver can manufacturer in India, for 50 years and counting. The caster wheels we design (including the latest Supremo Casters) – with their smooth mobility, enhanced reliability and top-notch load bearing capacity – make sure that sliver movements are uniformly smooth, and all risks of sliver damages are eliminated. After all, we are committed to serve our clients as a one-stop spinning solutions provider.
Also Read : Complete Guide on Types of Caster Wheels for Spinning Cans
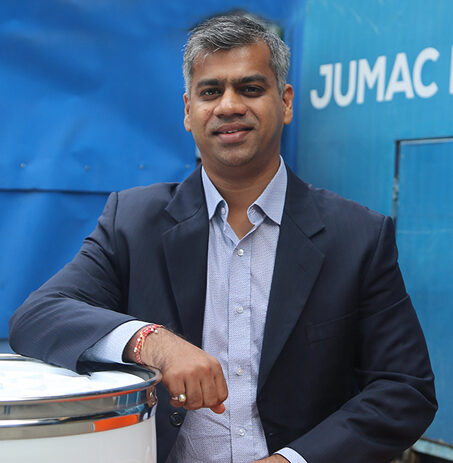
Passionate about transforming the industrial sector of textile and spinning industry with innovative solutions. Director at Jumac Manufacturing, leading spinning cans and accessories manufacturer and exporter from Kolkata, India.