Thanks to continuous research and openness to innovations, the Indian…
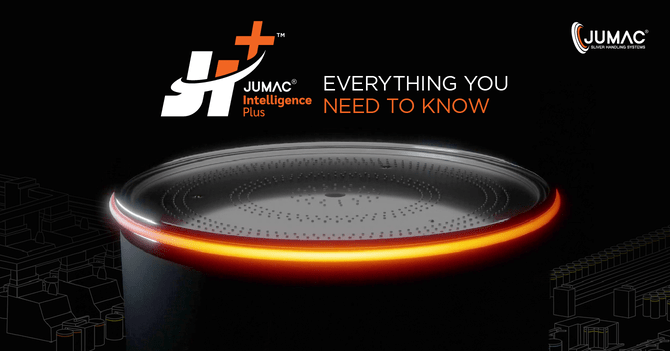
Ji+ Spinning Cans – Everything You Need To Know
Technology is changing the face of modern-day manufacturing facilities. The textile & yarn production sector is no exception to this. With demand levels surging and the need for optimising quality & productivity at an all-time high, adoption of Industry 4.0 tools and solutions is growing at a rapid clip at the top mills in India (and worldwide). As the top spinning can manufacturer in India, Jumac Manufacturing regularly launches innovative sliver handling solutions – that resolve the exact operational gaps and pain-points at spinning mills effectively. For us, it is always about finding ways to make spinning better.
At India ITME 2022, we unveiled the first look of our cutting-edge Ji+ technology. The concept is powered by the Industrial Internet of Things (IIoT), and has the potential to make the day-to-day operations at spinning mills truly smart. Here’s a roundup of all that you need to know about our revolutionary sliver management technology:
A Revolutionary Solution That Offers Last Mile Tracking
In the absence of real-time data, it is extremely tough for mill operators to ensure resource optimisation on the floors (both in terms of manual effort and inventory management / can performance). With Ji+, we are looking to resolve this problem, by creating a hive network that offers complete operations visibility and last-mile traceability. In relatively large spinning mills where thousands of cans are used, this type of ‘active identification’ is extremely important to pull up productivity levels consistently. Efficient lot management, in turn, also helps in identification of yarn deficiencies in a timely manner.
The Task Of Sliver Status Tracking In Cans Is Made Easier Than Ever
Manual errors and oversights can undermine the overall performance of mills in a big way. The Ji+ technology leverages the power of smart, data-backed automation, to eliminate such avoidable errors. This special range of cans have LED identification bands (or, ID bands) that indicate the exact sliver status in each spinning can – so that there is practically no wastage of time or effort. The blinking pattern of the ID bands show whether the cans are empty, full or nearly full. Actionable insights are generated, helping mill operators take immediate action (e.g., replacing an empty can).
Researches have shown that spinning cans may often lie idle on mill floors – due to lack of a reliable automated solution that shows the sliver status in them. Ji+ resolves this issue, and optimises the average Utilisation of Machines (UoM) figure.
Visual Identification To Rule Out Yarn Mix-Ups
The end-to-end visibility that Ji+ brings to the table also goes a long way in constant yarn quality monitoring on the floors. Since each and every aspect of spinning / yarn-making is put under the scanner, predictive maintenance emerges as a major advantage (in case there is any glitch at any manufacturing stage). Visual identification plays a key role here. Cans carrying fibres of different quality will have smart ID bands of different colours – ruling out possibilities of yarn mix-ups, and consequent quality degradation. By implementing the Ji+ technology, mills can make sure that sliver quality is never hampered due to fibre mix-ups.
Note: The LED strips of the Ji+ cans are available in up to 12 colours.
Centralised Control For More Informed Decision-Making
In the bid to live up to our billing as the top spinning can manufacturer in India, we keep pushing the boundaries – to establish a stronger sliver management ecosystem. With Ji+ (Jumac Intelligence Plus), we have taken things to the next level. The IIoT-powered technology makes use of automatic visual insights (based on artificial intelligence), which facilitates quicker and better material flow management at the mills. Since all the data generated by the system can be accessed & viewed on a centralised dashboard (as well as the smart devices of authorised personnel), there are no information gaps, and overall working capital efficiency is significantly boosted. In a nutshell, Ji+ makes it possible to monitor can usage and yarn manufacturing stages anytime, and from anywhere.
Elimination Of Uncertainties In Can Movements From One Stage To Another
At mills, one of the common problems is the feeding of ‘wrong cans’ in machinery. This issue can happen when the spinning cans move from one stage to the next. The Ji+ system has the capacity to generate alarms / indications that let operators know a mistake has happened, and corrective actions need to be taken. As a result, there are no uncertainties at any point. The constant movement tracking ensures that there are no delays in can replacement or related tasks.
In a primarily manual setup, there are risks of the ‘wrong cans’ being sent / fed into a particular section or machinery (carding, combing, draw framing, etc.). When this happens, the spinning machinery itself can develop glitches – leading to lengthy system downtimes and lost productivity. The enhanced traceability introduced by the IIoT-powered Ji+ spinning cans helps in keeping such problems at an arm’s length. As such, the quality parameters – and hence, the reputation – of mills are maintained.
The Compatibility Advantages
There are several renowned OEMs of spinning machinery (Trutzschler, Rieter, Saurer, LMW & more). To ensure that mill operators do not face any problems, each spinning can manufactured by Jumac is fully compatible with the different spinning machines by all OEMs. The Ji+ range of ‘smart cans’ is no exception to this. Irrespective of the OEM whose machinery is being used at a particular mill, our latest spinning automation technology can be easily implemented, to drive productivity and efficiency levels.
Yet another advantage of the Ji+ technology is its seamless compatibility with our Smart Can mobile app. In other words, by installing this application, users will be able to track real-time insights regarding can utilisation ratio, state of mill operations, and a lot more, while on the go.
Note: The Smart Can app is available for download on the App Store and Play Store.
A Robust Platform To Counter All Spinning Inefficiencies At Mills
Backed by dedicated research and best-in-class technology, the Ji+ system combines the capabilities of data-generating software with state-of-the-art hardware. Through superior visibility and actionable insights, all sliver movements in spinning cans can be tracked – right from the preparatory stages to the final phase of yarn spinning. This enables timely detection and removal of defects, which might otherwise be difficult to find out. Be it data management, or material handling insights, or inventories, or mill resource optimisation – the Ji+ technology has been developed to take care of all key variables at mills that affect the productivity figures directly.
Response At India ITME 2022
At Jumac, all our innovations are planned to resolve problems, and make life easier for our clients worldwide. The Ji+ technology is our biggest innovation yet – and last year’s edition of the ITME event was the perfect platform to unveil the first look of the technology, and the response we received was well & truly unprecedented. Our team received a lot of queries from clients from India and abroad. Our team of experts are working on the final stage of Ji+ development – and it can truly transform the operations of the textile & yarn sector.
Also Read : JI+ : Jumac Leads the Show at ITME India 2022 With Innovation
Shaping The Future Of Spinning
From tracking performance on an everyday basis, to safeguarding against idle can times and yarn mix-ups/mismanagement, the Ji+ solution has been designed to usher in a new dawn of systematic operations & efficiency at spinning mills. Real-time reports are generated by the system, delivering accurate, actionable insights to users – and helping them transform their mill operations. Cloud-based automation will shape the future of spinning, and with Ji+, we are helping our customers take the leap, with ease.
Different types of fibres – in terms of nature and quality – are handled at spinning mills. It is also extremely challenging (at times, impossible) to track the status of sliver in every individual spinning can manually. The onus is squarely on mill-owners and operators to move beyond the limitations of a labour-intensive industry – and that’s precisely where our proprietary Ji+ technology is expected to help in a big way. The role of automation in sliver handling will continue to increase, IIoT will be right at the heart of things, and we are ready to bring on the future of spinning!
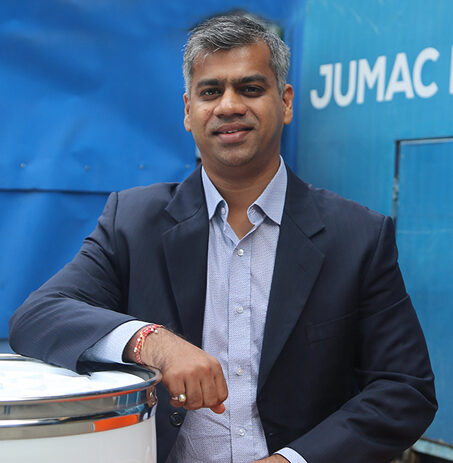
Passionate about transforming the industrial sector of textile and spinning industry with innovative solutions. Director at Jumac Manufacturing, leading spinning cans and accessories manufacturer and exporter from Kolkata, India.