In 2017, the value of the Indian textile industry was…
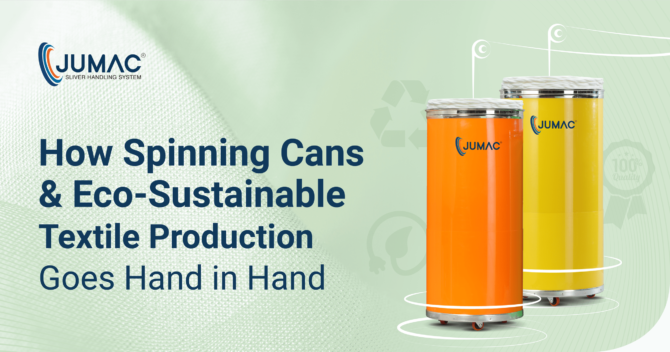
How Do Spinning Cans and Eco-Sustainable Textile Production Go Hand in Hand?
While the worldwide textile manufacturing sector is growing fast, we cannot (and should not) turn a blind eye towards the unprecedented sustainability challenges it brings forth. From significant waste generation and pollution of freshwater, to carbon emissions and environmental degradation, there are risks of different types associated with the operations in this sector. However, manufacturers of spinning cans as well as spinning mill owners can bring about a definite change in this context, through responsible & conscious actions and forging greater care for the environment. Over here, we will explain how the use of quality spinning cans and eco-sustainable textile manufacturing can potentially be in sync, always:
The Quality Of Fabric Matters; Sliver Integrity Is Of Utmost Importance
Selecting sub-standard HDPE spinning can and accessories can compromise the necessary sliver handling parameters. With damaged sliver, the final yarn/fabric also becomes of poor quality – leading to frequent tears, fading, and other visible problems. Such textile material has to be replaced frequently, necessitating more production, more raw materials, and more pressure on the environment.
To maintain the ecological viability of textile production processes at mills, using quality-optimised & versatile spinning cans is immensely important. Such sliver cans (made of virgin HDPE sheets) rule out possibilities of sliver imperfections (stretching, breakage, deflections, etc.). All material handling requirements are managed optimally – ensuring the generation of perfect-quality sliver. No quality glitches, no demand for additional resources, no burdens on the ecological system.
The Role Of Regular R&D Is Growing Bigger
In textile manufacturing, different types of chemicals and harsh materials have to be used. These can, potentially, pose challenges in the sustainability and environmental viability of the day-to-day operations at mills. This is where the importance of research and innovation comes into the picture. With the help of high-quality insulation materials, solar energy collectors, anti-polluting filters, water conservation & more, textile producers can ensure that the environment is not hampered in any way.
With textile technology evolving constantly, the need for dedicated R&D (and an openness to innovation) is no longer limited to only mills. Leading manufacturers of spinning cans typically pay attention to the product design factor – ensuring that there are practically no material wastes, all resources are used optimally, and the overall value chain of the textile sector remains intact. The onus is on these suppliers to take eco-sustainable actions for meeting the varying buyer requirements.
Recycling Holds The Key; For Mills & For Suppliers Of Spinning Cans
By the end of 2024, the value of the worldwide textile industry will soar past the 1230 billion mark – consolidating its position as the second-largest business sector globally. All stakeholders from the sector need to take up the responsibility of ensuring enhanced material lifecycles, reducing wastage, making use of agile & efficient production methods, and raising awareness about eco-sustainability in general. In addition, there has to be a system to track the results of ‘sustainable actions’.
The top spinning can manufacturers are getting increasingly involved in adopting the 3R strategy (Reduce, Reuse, Recycle) in their operations. Recycling, in particular, is being done as and when possible. For instance, the HDPE sheets can be recycled & reused – while waste/scrap materials can be reengineered to design relatively small components & accessories. Awareness about systematic waste disposal is growing as well. The raw materials for the HDPE spinning cans are being selected in a sustainable manner too.
Renewable Energy In The Textile Industry; A New Dawn
Investments on renewable energy applications are escalating, both in India and globally. In FY 2022, a staggering 15.5 Gw of renewable energy was added in the domestic sector. Such alternative energy sources can play a pivotal role in consolidating the eco-sustainability of the textile industry. There are already plenty of mills and other textile manufacturing facilities that are powered (at least to some extent) by solar power. The lighting systems are selected to ensure maximum energy efficiency as well.
In this context, widely trusted sliver can suppliers, like Jumac Cans, are also playing important roles. All spinning can manufacturing processes/machinery at these companies adhere to the latest technological standards. Alternative energy sources (particularly solar energy) are utilised as and when possible, and the different machines & equipment are regularly inspected, upgraded or replaced – to prevent operational costs from shooting up, and effluent generation becoming a major problem.
The Rise & Rise Of Sustainable Sliver Handling
Sustainability and/or ecological efficiency is not limited to any particular stage of textile spinning or sliver can designing. Rather, it has to be built-in as part of the business culture – where spinning mills make conscious attempts to rule out possibilities of sliver wastage at any stage. For this, mill-owners and machine operators need to understand the precise sliver management requirements, and set up their machinery & production standards accordingly.
In order to give shape to the vision of fully sustainable sliver management & handling, the best spinning can manufacturers design high-quality sliver cans of different sizes and diameters – so that they can be used to ensure sliver handling at all stages of spinning (carding, combing, draw framing, roving, open-end spinning, etc.). By eliminating the need for having to source spinning cans from different suppliers, the risks of using up too much of resources are being minimised.
A Journey Towards Better Tomorrows
It is very important to understand that every action taken by anyone involved in the textile sector (no matter how apparently small the action is) makes a difference. At the facilities of spinning can manufacturers as well as textile production units, things like tree-plantation, creation of recycled material for captive consumption/usage, minimising water and energy wastage, and maintaining a zero-pollution strategy are extremely vital. The focus has to be squarely on bringing about a systematic change, with environmental impacts brought down as much as possible.
Sustainability in textile production is often hampered due to problems in sliver transportation and/or packaging. That’s precisely why spinning cans with additional loading capacity (for extra sliver storage) and trolley cans (for smooth sliver transportation) are used at the top mills across the country. In addition, textile manufacturers have taken up the challenge of coming up with eco-friendly packaging solutions for their products. Textile logistics have become smarter and ‘greener’ as well. The textile industry in future will have a considerably lower carbon footprint, that’s for sure.
Across the world, concerns over swift environmental degradation are rising. It is high time that everyone, and stakeholders from the textile production sector in particular, wakes up to the challenge of prioritising holistic growth – one in which the ecological balance is not harmed in any manner. From mill operators to HDPE spinning can manufacturers, the responsibility to take care of eco-sustainability lies with everyone. After all, every conscious step – no matter how trivial apparently – makes a difference.
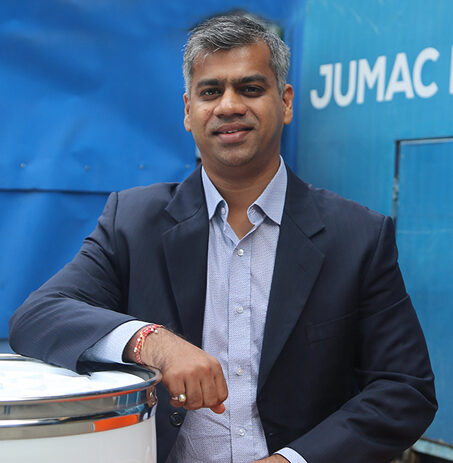
Passionate about transforming the industrial sector of textile and spinning industry with innovative solutions. Director at Jumac Manufacturing, leading spinning cans and accessories manufacturer and exporter from Kolkata, India.