The Indian yarn & textile industry makes up nearly 25%…
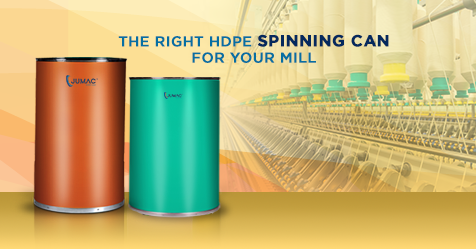
How to choose the right HDPE Spinning Can for your Spinning Mill
Products of Jumac have high demand not only in India but abroad as well. The modern sliver cans have multiple modifications to make them more suitable for the high-end spinning technology and machinery used in the modern spinning mills. Therefore, when you search for the right HDPE spinning can for your spinning mill, you need to keep several parameters in mind while making the choice. Here are some easy steps to follow in this regard.
Size
Even in a small-sized spinning mill, hundreds of cans are used to transport, accumulate and collect different forms of slivers. The HDPE (High-Density Poly Ethylene) spinning cans for the textile industry must be of a standard size and
consistent quality. The inside diameter of the can along with the total height – with or without caster – should draw your attention first. Starting from 225 mm up to 1200 mm in diameter, various sizes of cans are available along with the entire range of accessories. Make sure it comprises virgin HDPE sheet hardened and tempered precision springs, dust and fluff-free casters, standard stainless steel accessories and moulded plastic top and bottom covers to ensure a uniform material handling system to minimise imperfection in sliver handling.
Type of Machines
As there are several kinds of operating machines installed in spinning mills, the cans should be made suitable for carding, draw frame, combing, as well as the updated versions of rotor spinning. The strength and ability to undergo several processes with minimum wear and tear in the production chain defines the best
in terms of quality.
Top and Bottom Covers
When spinning, a huge amount of centrifugal force tends to affect the physical structure of the cans, making the cans prone to tilting and slipping. Make sure top and bottom covers are added to sliver cans. Manufactured from Poly Propylene Copolymer (Moulded PPCP), the top and bottom covers prevent slipping of the cans from their respective bases. The surface grip of PPCP must be strong enough to hold the cans in place. In order to improve durability and strength, Acrylonitrile Butadiene Styrene (ABS) is added to the top cover. Besides, the gap between the floor and the bottom of the can should be ascertained properly. There should be a minimal floor gap – 5mm to 20 mm – for open-ended cans. But for other cans with cover, the floor gap range can vary between 55 mm and 70 mm. The spinning cans you choose must carry these features.
Top Rim and Band
At the brim of each sliver can, there is a rim made of SS (Stainless Steel) which is replaced by Galvanized Steel (GP) now. The top rim upholds the shape of the sliver cans to prevent them from developing cracks and collapsing when rotating under high speed.
Bottom Rim and Plate
There should be an additional support plate – GP plate obtained from heavy duty power press – at the bottom of the sliver cans. Additional ribs and contours hold the balance of the cans. The bottom rim has caster fittings or is connected to caster adapters. Along with the rims, the bottom plate increases the longevity of the sliver cans – allows perfect adjustment to the toothed belts. The springs are also supported by the top rim and the band to safeguard the sliver from the pressure of the spring during rotations.
Identification Bands
All HDPE cans of similar height, colour and diameter are indistinguishable. Different colours of PVC based identification bands at the topmost border of sliver cans provide an attractive appearance. Besides being a medium for identification, the bands act as shock absorbers and make the cans strong. PVC is a highly stable material and gives adequate rigidity to the sliver cans during bumping or other handling conditions.
Springs
Check the pre-tension of the spring to ensure it is minimal before the commencement of loading the cans. Correct spring load of the cans depends on the kind of fibre to process, sliver length, sliver hank and the total weight of the
sliver to process.
As a result, all cans should have a perfect coiled spring manufactured from high carbon special steel wire. Heat treatment ensures the springs have uniform load bearing capacity while being auto-adjustable to sliver pressure. The springs provide unparalleled support and maintain a horizontal position. These springs can be calibrated as per height requirements. Irrespective of the load and other surface tensions, the sliver can has smooth uniform doffing and perfect castor fitting. Best quality springs are lightweight, rigid, and anti-corrosive. Two major types of hardened and tempered precision springs are manufactured for sliver cans by Jumac. Box spring is suitable for cans of HDPE sheets of varying thickness. The springs are heat treated, and also possess anti-rust properties. The pantograph springs are high stability springs that ensure that the sliver cans maintain balance irrespective of the sliver load. High-quality pantograph springs have electro-welded galvanized (GP) shutters that take up an even crisscrossed shape. This mechanism is supportive of uniform spring movement while upholding a constant sliver height. This hardened and tempered type of spring for sliver cans is known for its capability of retaining original properties of sliver at all stages. Sliver cans with box type spring are more effective for maintaining desired sliver height during rotor spinning. The springs are attached to the top and bottom parts of the sliver cans to eliminate sliver wastage while adjusting with altering pressures of sliver. Without springs, sliver cans for the textile industry cannot produce desired yarn quality. One should know the advantages of each kind before making the decision.
Caster wheels
Ensure caster wheels never get entangled with dirt or corrosive chemicals that are used for yarn production. PP (Polypropylene) and Nylon 6 are popular variants chosen as the raw material for manufacturing caster wheels.
Customized caster wheels as per the requirements of customers should be available. The caster wheels with a zinc-coated body for easy mobility to the sliver cans during different production stages are preferred. Jumac excels in the production of these as well. From sliver formation to fiber collection to yarn take-off, the role played by sliver cans is versatile. With the introduction of high-tech equipment in the spinning industry, maintenance and quality of the sliver can has become a priority. Apart from the quality of HDPE (high-density polyethylene) used to manufacture the sliver cans, whether the cans are in optimum running conditions or not depends totally on the spares and accessories. Prefer a brand that offers this and lots more.
If you assess carefully, Jumac cans are born to deliver unmatched performance on all the vital parameters – Just Make Best.
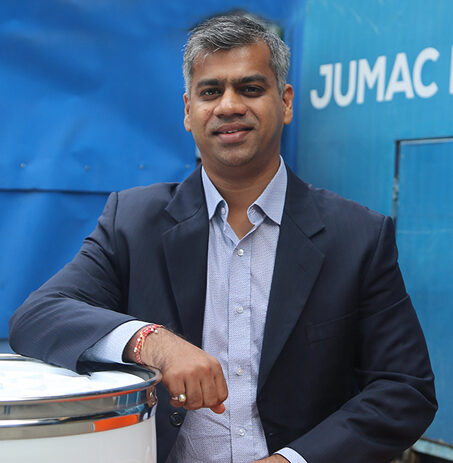
Passionate about transforming the industrial sector of textile and spinning industry with innovative solutions. Director at Jumac Manufacturing, leading spinning cans and accessories manufacturer and exporter from Kolkata, India.