Caster wheels are important as they ensure smoother movement of…
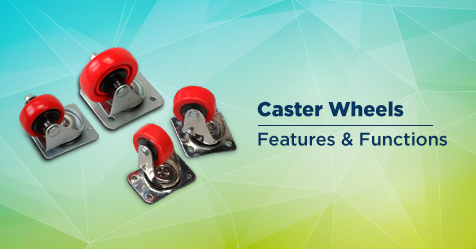
How are Caster Wheels Chosen for Sliver Cans
Features & Functions of Caster Wheels
Caster wheels are used in multiple industries to transfer heavy and light materials across the production plants. The transportation equipment usually comes with caster wheel fittings. For easy rolling experience, several properties are added during the production of caster wheel.
For sliver cans, caster wheels of smaller diameter are preferred. This is primarily because of two reasons. Firstly, bigger caster wheels increase the risk of sliver wastage, as when the wheels get stuck, the containers can tip off or tilt. Sliver cans that are filled to the brim have an increased risk of sliver tumbling over if the person concerned fails to control the big caster wheels. Secondly, if the caster wheels are large, they will need bigger size fixtures, which in turn, will increase the cost.
There are two types of caster wheels- swivel caster and rigid caster. While the swivel caster wheels allow movement and rotation in all directions, the rigid caster wheel moves in one particular direction only. The fact that the swivel caster wheels can rotate 360 degrees even under fully-loaded condition makes them the common choice in the spinning industry as the same sliver cans goes through different stages for production of cotton yarn and hence requires a lot of movement within the production plant.
Challenges faced:
The two biggest challenges in the use of caster wheels in the spinning industry are – the heat and dirt. The machinery used in a yarn spinning mill, like draw frame, carding, and combing machine, leaves single fibers of un-spun cotton suspended in the air. These fibers then settle on the floor that is sometimes filled with corrosive materials, thereby forming the tar-like dirt that poses as floor obstructions when the sliver cans fixed with caster wheels are rolled on. The dirt makes it difficult to rotate, seriously disrupting the overall transportation procedure. This is why sometimes the swivel caster wheels have an optional braking system.
What determines the quality of caster wheels:
The type, i.e. the construction material of the caster wheels is judged based on these features- tear strength, tensile strength, and abrasion resistance. The more the construction material is able to maintain these, the more productive the wheels become. The sliver cans are usually exposed to different handling conditions. An ideal caster wheel must be able to endure all those.
The construction material of the caster wheels needs to be highly heat-resistant as the sliver cans are fitted in the machinery with the caster wheels. If the construction material of the caster wheels are not heat-resistant, the heat generated from the machines could alter the shape and size of the caster wheels, thereby making them unfit for operations.
In general, the caster wheels made from both PP (Polypropylene) and Nylon 6 are the best. They enhance durability and functionality of sliver cans like no other. At the same time caster wheels made from PP and Nylon 6 also provide support to the bottom plate and rim of the sliver can. For maximum durability of caster wheels, these specific factors must be controlled- floor conditions, load amount, exposure to corrosive chemicals, the frequency of use, exposure to heat and moisture, and speed restrictions.
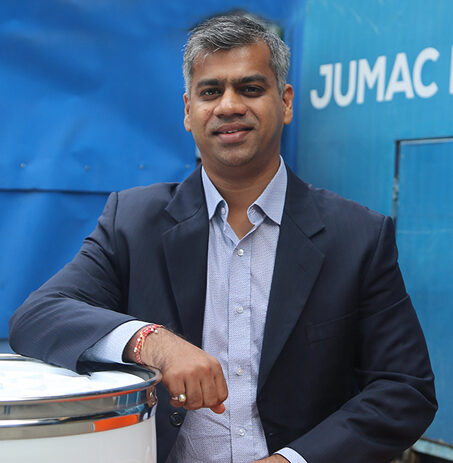
Passionate about transforming the industrial sector of textile and spinning industry with innovative solutions. Director at Jumac Manufacturing, leading spinning cans and accessories manufacturer and exporter from Kolkata, India.