The unwavering focus of Jumac on making textile spinning processes…
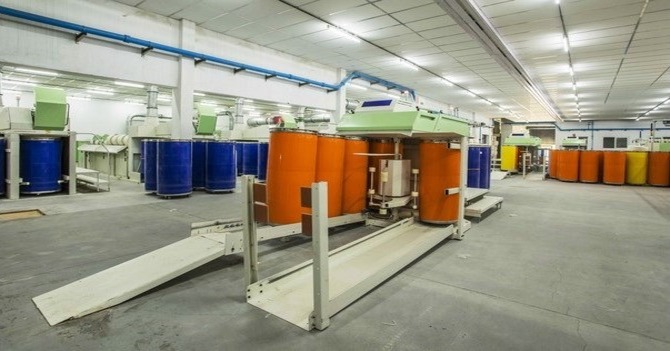
Effects of Defective Spinning Cans on the Performance of Spinning Machinery
Every textile mill looks to optimise the quality of the yarns it produces. However, if the spinning cans being used on the mill floor are defective, that can throw a spanner in the works. Apart from damaging original sliver parameters and final yarn quality, can defects may – over time – affect the functionality of spinning machinery as well.
Before elaborating on the knock-on effects that crop up when sub-standard or defective sliver cans are used, it is important to have an idea about the common types of can defects. From problems in the HDPE sheet welding and incorrectly fixed bottom plates (which, in turn, causes can tilting), to selection of the ‘wrong’ spring load, sub-standard caster wheels & more – there can be a myriad of problems in cans that are not up to the mark. We will here elaborate on the issues that can crop up as a result of using defective spinning cans:
So, How is the Performance of Spinning Machines Affected by Problematic Spinning Cans?
Continuous usage of defective cans (and sliver handling systems, in general) affect sliver quality and spinning efficiency in diverse ways. Let’s examine these potential problems in greater detail:
Problems at the Carding Phase
For optimal performance and longevity, carding machines have to be used with spinning cans that are absolutely glitch-free. Several types of problems can, however, crop up at this stage. For instance, if there is accidental can tilting, both the silver coils AND their quality are hampered – causing higher-than-acceptable volumes of sliver wastage (at the time of unwinding at the creel zone). The efficiency of the carding machines is also likely to deteriorate, since creel breakages are higher. There are loading problems and resultant production stoppages.
Not selecting the correct spring load in the spinning cans also leads to a host of problems – related to greater unevenness in the relatively lower coils of the sliver. Both the CVm% and U% of sliver goes up, affecting the final quality.
Using sliver cans with jammed / damaged caster wheels is also not recommended. Such casters inhibit the smooth transportation of the cans on mill floors. As a result, labour fatigue levels go up, and delays happen.
Problems During Breaker Draw Framing
Once again, if the spring load of the cans is not appropriate, they can pose problems at the breaker draw frame. Since the U% increases significantly, the overall quality of sliver automatically goes down.
The Lap Forming Machine is used to receive the sliver from breaker draw framing cans, and prepare the laps for the next phase (combing). When the spring load of the cans is erratic or unstable, there can be considerable rise in the weight of sliver in the creel zone (of the lap former) – as a result of which sliver stretching, a commonly encountered yarn imperfection, happens.
In addition to the sliver stretching, the risks of breakage can also go up exponentially in the creel zone. Since the number of pieciengs are more due to the defective cans, the lap quality gets adversely affected, labour load increases, and the consequent loss of production time / quality is likely to be significant.
Problems at the Combing Phase
At this point, it is important to understand the difference between carded sliver and combed sliver. The latter is a lot heavier / bulkier than the former – and as such, the spring load of the comber cans also needs to be higher. Now, if this load is not set up correctly, the fibre-to-fibre cohesion is not maintained at the requisite levels, risks of sliver breakages and damages are more at the finisher draw frame creel zone. The higher the volume of these sliver breakages, the greater is the number of pieciengs, labour loads, and overall faults / inconsistencies in the sliver. When this happens, the comber machine itself starts to lose efficiency – and its performance starts to gradually go down.
Lack of stability is a common problem in defective spinning cans. This, in turn, can easily cause the cans to get tilted – thereby making the can movements inside the coiler system wobbly and non-uniform. In addition to the U% and CV% of sliver going up as a result of non-uniform can movements, there are more entanglements in the sliver as well, along with associated coil damages.
Problems During Finisher Draw Framing
As already pointed out earlier, the fibre cohesion levels in combed sliver is relatively low. On top of that, if the can springs are defective (i.e., the spring load is inaccurate), the sliver strength is affected – since the spring load is not enough to maintain the top-level sliver coil at the same level with the can top. As a direct result, sliver starts hanging with its own (unsupported) weight. Since the sliver separation is increased and the stretch percentage is higher, the quality of the final yarn is compromised.
The spring load of spinning cans has a direct impact on the U% and CVm% of sliver. When there are problems in this load, thin faults crop up, the CV% rises, and there are more breakages in the speed frame creel zone. This happens because the gap between the creel and the top coils of the sliver becomes higher.
Problems at the Roving Phase
By now, it is pretty much evident that spinning cans with incorrect spring loads can cause a lot of problems – both in terms of output quality and mechanical performance. In addition, if the storage time of sliver in the cans is higher than required, that also causes greater unevenness, and higher CV% (strength & count). The roving quality, as a whole, goes down.
When the spring load of cans is lower than the required level, problems come up in the winding phase as well. From CM cuts and CCM cuts, to CP cuts and CCP cuts – all the counts go up when the springs are old and / or do not have the ‘right’ load. When the spring load is correct, there is much greater assurance regarding sliver strength.
How can Jumac Manufacturing Help in Eliminating these Problems?
As an industry-leader from the field of sliver handling, we bring a combination of world-class technical acumen and the most advanced tools & solutions, to rule out possibilities of can defects (and resultant problems in mill performance). All products are designed at our state-of-the-art manufacturing unit – and we provide detailed spring load suggestions, so that there are no uncertainties. Spinning cans, trolleys, and all other accessories are manufactured in-house, and in adherence to stringent quality parameters.
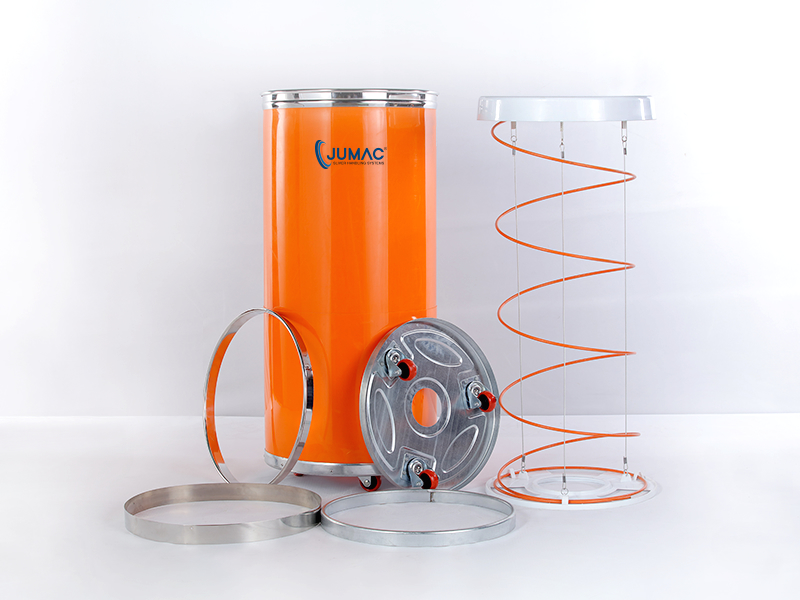
At Jumac, a systematic and highly reliable method is followed for assembling the cans. As such, can tilt risks are minimised (since the bottom plates are securely fixed). The anti-static HDPE sheets used in the can bodies eliminate risks of static charges, while the nylon caster wheels (with SS frame) come with complete dust-free and fluff-free assurance. As a result, can movements are smoother and operators can work with them more easily.
Many instances of yarn quality mismatches and gradual deterioration in the performance of spinning machines can be attributed to continuous use of defective spinning cans. It is always advisable to source these cans from a reliable & reputed sliver can manufacturer – while having the cans inspected (for probable damages, wear & tear, etc.) is of paramount importance too. Malfunctioning cans can result in the entire sliver handling system getting compromised – and in the increasingly competitive landscape of today, mills simply cannot afford that!
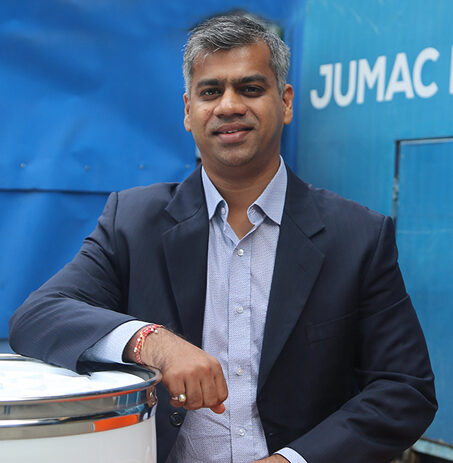
Passionate about transforming the industrial sector of textile and spinning industry with innovative solutions. Director at Jumac Manufacturing, leading spinning cans and accessories manufacturer and exporter from Kolkata, India.