This June, Jumac will be heading to Milan, to participate…
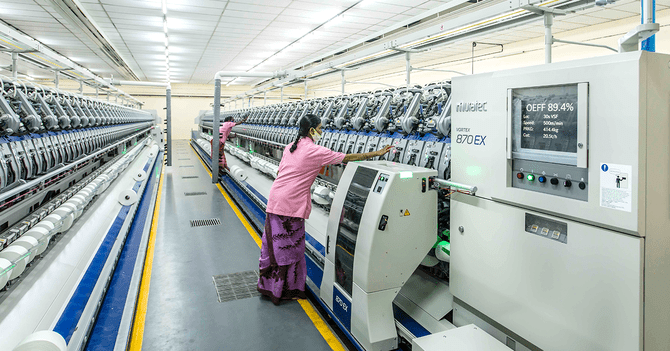
5 Safety Hazards in Spinning Industry and How to Prevent Them
Risk analysis is a vital component of managing a textile mill optimally. By understanding all probable (and commonly encountered) risks on mill floors, and taking the requisite action to eliminate them, production downtimes can be significantly reduced, resource wastage minimised, and consistent yarn quality maintained at all stages. Apart from working with the best spinning cans and spinning machinery, having a clear idea of these hazards is important, along with the knowledge of how to counter them. Let us here deliberate on these textile industry hazards in detail:
Problems While Handling the Compressed Bales in Godowns / Storehouses
On average, the weight of one bale of cotton can be up to 250 kgs. Now improper handling can lead to these bales falling down. This risk is particularly high when bale stacking is not done properly – and hence, the desired equilibrium is not maintained. Since forklifts are generally used in the godowns, there are also chances of risks occurring from faulty forklift movements. The cotton bales often have straps with rather sharp edges, making them a potential source of hazard as well.
While the risks seem serious, they can be eliminated simply by making the bale-handling and forklift-management in godowns more efficient. Every stack should ideally be double-checked, to ensure that they are not likely to fall. Ideally, the workers at this stage need to be trained well – so that they can handle the tasks with greater knowledge and expertise. While using the forklifts, it is vital to check that there is no smoke, and the wiring is properly done.
Problems During the Blowroom and the Mixing Stage
In the blowroom, there are many parts of the transmission machines – like shafts, belts, gears, pulleys, beaters, revolving components & more. Any problem in these components is likely to cause mechanical failure / sub-optimal performance. During mixing (i.e., when the cotton bales are opened and blown), the cotton bale can accidentally get opened (more likely when the steel straps are damaged / loose), posing a safety threat. At the time of dust removal from under the beaters too, there can be problems.
To manage these hazards in the best possible manner, all the machines used in the phase (bale breakers, hopper openers, condensers, beaters, assembly systems, etc.) have to be inside proper enclosures (when not being used), and interlocking is necessary for all the transmission machine parts that might be dangerous. There should also be provisions for emergency stopping and shifting (safety belt). In case a problem does crop up, a mill should have the arrangements for taking the required corrective measures.
Problems at the Time of Carding and Combing Stages
The risks during this stage mostly arise from malfunctioning carding machines or any component thereof. In particular, if the interlock guard is problematic (in the cylinder), that can lead to serious hazards. There are many instances of the transmission parts being kept unguarded, and gear problems remaining uninspected for extended periods. Improper maintenance of the licker-in system, the calendar roll nip and / or the doffer can also cause the process as a whole to be adversely affected.
The cylinder door (i.e., the stripping door) has to be double-checked, to eliminate risks of opening when the cylinder is moving. The functionality of the licker-in panels also need to be periodically inspected. The interlocking arrangement should be secure enough to rule out possibilities of access to the needles of the cylinder. The clearance space (gauging) between the flat, cylinder and licker-in components also have to be set up accurately. The parameters of the carded sliver have to be examined too.
Problems in the Draw Framing and Speed Framing
While productivity levels can drop due to sub-optimal usage / incorrect choice of sliver cans at this stage, the more common hazards are generally mechanical in nature. In the draw frames, the calendar rollers can easily get jammed, while there can be glitches in the head stock gears and / or the interlocking setup as well. At the time of fluff-removal, there are chances of unexpected flyer hits, causing injuries. When the pinion or the lifter rack is not maintained well, that can also cause complications.
The safety hacks for this stage also revolve around responsible machinery handling and attention to detail. For example, the flyer rotating zone needs to be carefully interlocked, and the gears have to be guarded in the recommended manner. In the speed frame machine, fencing has to be done for the gears present in it. By regular cleaning, risks of roller jamming can also be minimised. To maintain the requisite sliver strength, twisting is required (prior to roving) – so that the final yarn quality is not affected. The process of rock lifting and falling should also be smooth.
Problems at the Ring Frame Stage
A myriad of hazards and safety risks can come up in the ring frame stage of textile spinning. These range from accidental contact with bobbin edges (which are sharp), problems in the broken-end piecing process, sudden fall of bobbins from the creel, to improper bobbin handling, and even knife- accidents (which can occur at the time of fluff-removal from the rollers). Broken spindles can also be a reason for sub-optimal operational efficiency.
To avoid injuries in the ring spinning stage, being mindful about probable finger injuries (say, when operators hold the bobbins) is of immense importance. That’s precisely why putting on finger caps has become a mandate at practically all leading textile mills. It is also vital to check the working condition of the spinning machinery – and the spindles in particular at regular intervals. Dust and fluff-removal should be done in adherence to all stated safety parameters. Easy access to the bobbin-holder has to be ensured too, so that workers do not step into the railing section. The bobbin edges also require careful handling.
In addition to the mechanical / operational problems cited above, there are other occupational health hazards in the textile industry that mill workers need to be wary of. The presence of (often excessive) fibre dust on the floors can lead to a myriad of problems – while there can be safety risks during the material handling phases (particularly if the workers are not trained and/or do not use the proper protective gears). Not sourcing spinning cans from a reputed sliver can manufacturer company is also a mistake. The textile industry of India has immense growth potential – and the onus is now on mill-owners as well as OEMs to take bold, informed steps to cut down the prevalent risks as much as possible.
Continue Reading : From Sliver To Yarn – The Complete Yarn Spinning Process You Need to Know
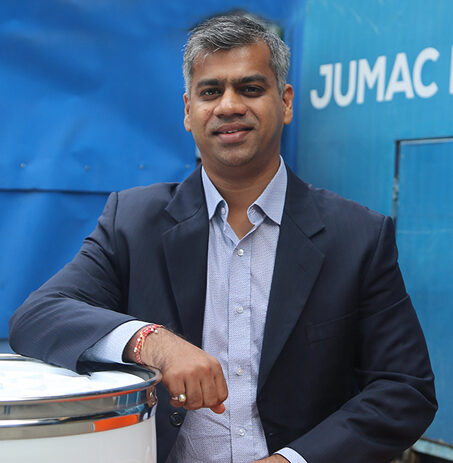
Passionate about transforming the industrial sector of textile and spinning industry with innovative solutions. Director at Jumac Manufacturing, leading spinning cans and accessories manufacturer and exporter from Kolkata, India.