Over five decades of our journey, we have mastered spinning…
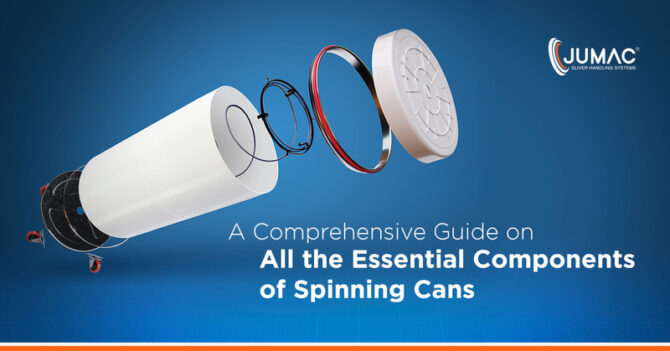
A Comprehensive Guide on All the Essential Components of Spinning Cans
Yarn-making is a delicate affair. Even apparently minor mistakes or glitches in sliver handling can adversely affect the overall yarn quality. Mills need to be wary about the efficiency and compatibility of the spinning machinery and sliver cans they are using as well. Given the fact that mechanical problems can lead to lengthy downtimes and production losses – it is only natural that any top spinning can manufacturer attempts to go that extra mile to ensure optimised sliver management through its solutions. The importance of using pre-tested, quality-assured components in spinning cans is paramount in this regard.
Over here, we will take you through all the key parts, components and accessories of sliver cans:
Virgin HDPE Sheet
For optimal performance and enhanced longevity, sliver cans need to adhere to specific quality standards. The role of the smooth virgin HDPE sheets (high density polyethylene) is important for this. HDPE is highly versatile, has excellent thermal-resistance, and ability to withstand mechanical impacts. The fact that the HDPE sheets used in the surface have powerful anti-static properties (to repel static charges) also adds to the reliability and operational efficiency of the cans.
The smooth finishing of the HDPE sheets rules out possibilities of the sliver getting damaged in any way. The cylindrical integrity of the spinning cans is also maintained – so that can movements and handling become smoother. Sliver can suppliers also ensure that the HDPE sheets they use have robust tensile strength for longer use.
Caster Wheels
In the context of sliver handling, the importance of ensuring smooth sliver mobility on the mill floors simply cannot be overemphasised. For this, leading spinning can manufacturers fit their products with durable, resistant and precision-engineered caster wheels. These wheels typically have fluff-free and dust-free designs, and do not come with any significant maintenance requirements. Casters are generally made of Nylon 6 or high-quality polypropylene (PP).
In order to enhance the average lifecycle of caster wheels in a spinning can, manufacturers use zinc-coated, high-pressed bodies on them. To meet the varying requirements of spinning, casters have a wide range of fitting options (for the base plate). Apart from casters for regular spinning cans, suppliers also design specialised caster wheels for trolleys. The load capacity and the wheel diameter of the wheels need to be checked carefully before purchasing.
Springs (Box-Type and Pantograph)
Often ‘touted as the heart of a spinning can’, springs ensure uniform stability of the sliver during high-speed spinning operations. Special steel coils, with high carbon content, are used to make the box-type springs. On the other hand, pantograph springs have a crisscross structure and have mild steel (or, MS) shutters. Prior to fitting in the cans, the springs are hardened and anti-rust treated. Thanks to the high dimensional accuracy of the springs used, the overall capacity of the sliver cans also goes up.
The slightest of spinning glitch can lead to a wide variety of sliver imperfections. These risks are kept at an arm’s length by springs that come with zero-tilting assurance. Calibration is done carefully, to make sure the requisite sliver weight is supported properly. Also, the portion of the top plate of the cans is maintained by the calibrated springs, which do not lose their shape over time.
Bottom Rim and Bottom Plate
The rims and plates of spinning cans lend additional protection to the sliver in them. A reputed spinning can manufacturer generally uses galvanised (or, GP) bottom rims and plates in their cans – precisely for this purpose. Strong contours and ribs (for better grip) are designed through heavy-duty pressing. These ensure superior fatigue-resistance and rules out the need for frequent replacements.
Top Rim and Top Band
When spinning cans are not of the desired quality, they tend to get deformed after repeated usage. In particular, their cylindrical structure gets affected. To avoid this, the top manufacturers & suppliers use galvanised and/or stainless steel top bands and rims that are instrumental in maintaining a firm grip on the cylindrical spinning cans.
Note: To protect a spinning can from getting damaged during the removal or insertion stage, spring bottoms – made of industry-grade moulded polypropylene – are used.
Top Cover and Bottom Cover
Slippage is one of the most common causes for sliver rupture and resultant imperfections. Polypropylene copolymer (moulded) is used by the best can manufacturers to design the bottom and top covers. Since chances of slipping are more or less eliminated, there are no risks of the sliver getting damaged in any way. In other words, these covers ensure better material handling. When the covers are strong enough, the level speed of sliver increases as well.
Identification Bands (ID Bands)
In relatively large spinning mills, manual errors can lead to the wrong spinning can being fed to a spinning machine (during carding, combing or drawframing). This, in turn, leads to mechanical downtimes and loss of operational efficiency. To counter such possibilities, polyvinyl (PVC) identification bands are used on the cans. Apart from managing the shock levels during can bumping and eliminating risks of can handling mistakes, these bands ensure accurate sliver count differentiation. These are available in multiple colours.
Sensors
Even when a set of cans sit idle in a large spinning mill, they can remain undetected. This represents a wastage of resources, with capacity utilisation becoming sub-optimal. This happens primarily due to a lack of centralised control, overdependence on manual effort, and an inability to track sliver status on a continuous basis.
While it is not mainstream yet, sensor technology can play a big role in plugging this gap. With the help of data-driven automation and timely, actionable insights, mills can take up the efficiency and productivity levels manifold.
Note: At the upcoming India ITME 2022 at Greater Noida, Jumac will be unveiling Ji+ Spinning cans – a breakthrough IIoT-based sliver handling system.
The Indian spinning sector is currently showing robust strains of growth, with close to 2 lakh spindles being prepared on a monthly basis. To keep up with the skyrocketing demand volumes, the onus is on mills to steadily increase their productivity levels – and using reliable spinning can and related accessories is essential for that. Over the next few years, the role of automation in spinning is set to go up – and it will be interesting to see what technologies the top sliver can manufacturers manage to come up with, to deliver the best results to their customers.
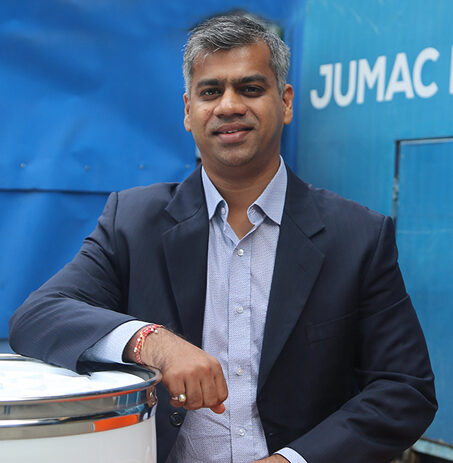
Passionate about transforming the industrial sector of textile and spinning industry with innovative solutions. Director at Jumac Manufacturing, leading spinning cans and accessories manufacturer and exporter from Kolkata, India.