There is a definite lack of sync between the trends…
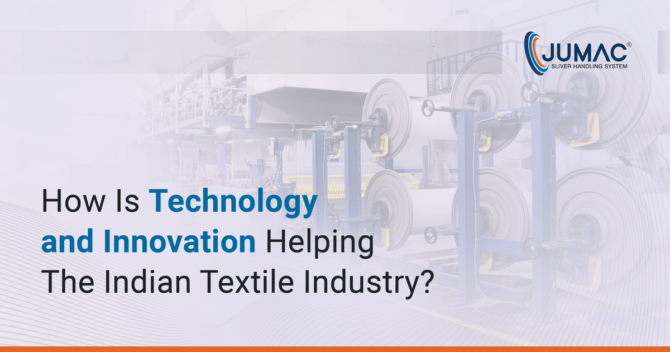
How Is Technology and Innovation Helping The Indian Textile Industry?
The legacy of the Indian textile industry is one for the ages. The origins of textile production in the country can be traced back to the Indus Valley Civilisation, while modern textile manufacturing in India started in earnest in the first half of the nineteenth century. Since then, the sector has come a long way – and it currently contributes nearly one-third of the total annual exports of the country. The importance of textile manufacturing in the Indian industrial scene is growing exponentially too, accounting for almost 5% of the Gross Domestic Product (GDP) figure.
Technology and innovation have been key drivers in the evolution of the Indian textile industry over the years. As spinning machinery & tools are becoming more sophisticated (with automation playing an increasingly vital role) and agile production methodologies are being seamlessly adopted, mills are successfully boosting operational efficiency and productivity levels. Leading spinning can manufacturer companies are also doing their bit, to ease material handling on mill floors, rule out possibilities of sliver imperfections, and ensure the production of the finest-quality yarns. Over here, we will briefly look at how technological advancements are taking the textile industry in India to the next level:
The Spinning Process Is Becoming Technologically Efficient
The process of creating yarns from fibre, and fabric from the yarn, used to be predominantly manual in the years preceding the industrial revolution. However, over the last 2-3 decades or so, spinning mills have really proliferated – both in India and abroad – and automation has come to play an increasingly vital role. In fact, technology has helped mills in meeting the unique spinning requirements of natural fibres (jute, cotton, etc.) and man-made fibres. The conventional methods of ring spinning are gradually making way for compact spinning technologies. That, in turn, is paving the way for better yarn strength and optimised productivity.
Spinning Machinery Are Evolving; Sliver Handling Is Becoming Smarter
While production speeds and turnaround times were low in the early days, a high point was the quality and the minute detailing of slivers & yarns. With the help of cutting-edge spinning machinery from leading OEMs (Trutzschler, Rieter, Marzoli, LMW, Saurer and others), mills have been able to take up production standards manifold – while the speed & scale of manufacturing have skyrocketed as well. Going forward, as the machine infrastructure becomes smarter, the precision, resilience and quality of textile production will go up further.
In addition to the machinery used in textile mills, spinning can technology is also making a difference. The top manufacturers of sliver cans & related components are using premium-grade material to design spinning cans of robust designs, powerful resilience, and excellent usability. Most importantly, the availability of sliver cans that are fully compatible with all spinning machinery brands is taking up the convenience factor. This spares mill-owners the worries of mechanical glitches and related hassles.
The Role Of 3D Printing Is Growing
Openness to innovation has emerged as a common trend among the leading spinning mills in India. 3D printing is gradually finding application in different phases of textile & apparel productions. It has to be taken into account that 3D printers can be applied only on fibres that have a certain level of thinness and resilience. This technology is, of course, still at a developmental phase – but considerable time & effort is being invested to make it more mainstream in yarn production processes over the foreseeable future.
In this context, the rising popularity of digital printing in textile manufacturing also warrants a special mention. Thanks to this technology, the entire yarn processing system has become significantly more flexible – particularly when it comes to adding print motifs on clothes. Textile designing is becoming more unique and customised over time – helping buyers find and select products that deliver the best value for money for them.
Sliver Imperfection Risks Are Being Eliminated
Sliver is delicate. Mistakes in sliver management – however miniscule it might seem – can lead to irreversible damages in yarn quality. Leading spinning can manufacturer companies, like Jumac Cans, are constantly striving to rule out possibilities of common sliver imperfections – like sliver breakage, stretching, deflections and other related damages. The smoothness of the spinning can surface (HDPE sheets are generally used) is key for this, as is the enhanced stability and reliability assurance. Components like fluff-free caster wheels, can springs (box/pantograph), top & bottom rims, bands & more ensure superior performance and greater material handling ease.
Manufacturing Technologies Are Undergoing A Complete Digital Transformation
Technology and innovation has revolutionised the day-to-day operations at spinning mills in the truest sense. Apart from spinning machines and sliver cans, digital technologies are helping the journey of the Indian textile sector from a labour-intensive to an automation-intensive industry. Machine control, usage and maintenance have become smarter and more systematic as well – with analytics, data storage and artificial intelligence playing crucial roles. Given the escalating demands for high-quality yarns, mills are consistently endeavouring to scale up productions and ensure smooth supply chain operations. In addition, textile manufacturers are increasingly moving to data-driven operations – to ensure full quality optimisation and glitch-free customer service.
Nanotechnology and Pleating Technology
Amid the growing concerns over environmental degradation across the world, sustainability has become a watchword for the textile industry. This is where the importance of state-of-the-art nanotechnology comes into the picture. Through seamless implementation of nanotechnology, mills are being able to make their manufacturing processes more energy-efficient, water-resistant, and even low-maintenance. At a time when everyone is talking about energy thresholds, nanotechnology is doing its bit to boost sustainable operations.
In the predominantly manual textile manufacturing processes, there was practically no scope for pleating (or the production of knitted fabrics). Things have changed with the constant advancements in technology – with modern machinery making pleating possible. Knitting machines are also being used on a large scale, contributing to the evolution of the textile & apparel industry.
Note: Radio-frequency identification (RFID) and robotics are also gradually emerging as key elements in the digitisation of the textile production sector.
The Focus On Quality Is Growing Stronger Than Ever
As the Indian textile industry is maturing, the levels of competition are also escalating. In order to survive and thrive in the present-day world, textile manufacturers are increasingly relying on a wide range of testing machinery for ensuring optimal quality of output. Such machinery includes fineness testers, strength testers, yarn testers, count balance tools and more. Top spinning can manufacturer companies are also on the lookout to expand their portfolio with diversified material handling solutions (e.g., trolleys, crates, jute spinning cans). The onus is on spinning mills and textile producers to maintain a balance between speed, quality and expertise – and technology is helping them do precisely that.
The Rise & Rise Of Mobile Technology
As the Internet of Things (IoT) continues to strengthen its hold, and the volume of smartphone-users keeps increasing by the minute, mobile technology is finding increased acceptance among textile industry stakeholders. In the ‘connected world’ we live in, mobile applications can go a long way in minimising service concerns and ensure fast and smooth information transfer across all relevant parties. For instance, a dedicated mobile app can make the process of ordering sliver cans easy and worry-free. Tracking order status and/or checking product specifications, while on the go, is facilitated as well.
A CAGR of over 10% (for the 2020-2026 period) clearly underlines that Indian textile & apparel manufacturing is well and truly on the fast track of growth. Within the next four years or so, the value of this industry is projected to soar to nearly $195 billion. Probably the biggest reason behind this remarkable growth is the widespread adoption of smart spinning can technology – which has become central to the robustness of the sliver handling ecosystem in the present-day world. As things stand now, it won’t be wrong to refer to the ‘textile sector’ as the ‘tech-stile sector’!
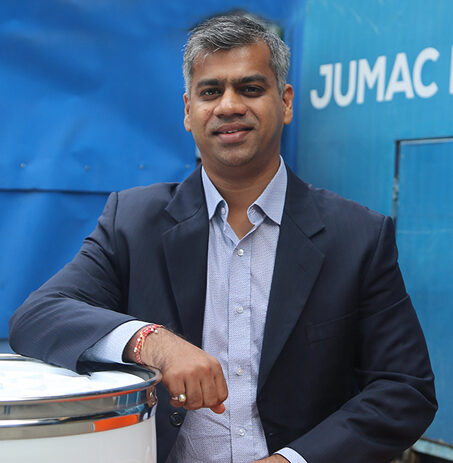
Passionate about transforming the industrial sector of textile and spinning industry with innovative solutions. Director at Jumac Manufacturing, leading spinning cans and accessories manufacturer and exporter from Kolkata, India.