For many spinning mills across the world, mechanical downtime causes…
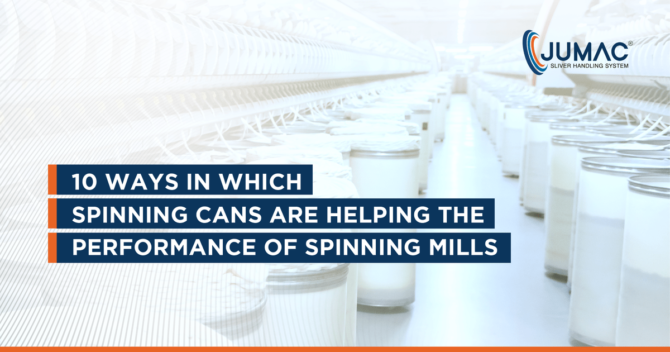
10 Ways In Which Spinning Cans Are Helping The Performance of Spinning Mills
The challenges faced by spinning mills in the present-day world vary widely. From poor productivity levels due to inadequate/sub-optimal use of available resources & technology, to concerns over sliver imperfections and yarn quality – there are multiple problems to be tackled on a day-to-day basis. Using outdated or damaged HDPE spinning cans also leads to operational glitches cropping up. We will here highlight how the best spinning cans help in bolstering the overall performance of spinning mills:
1. Right Spinning Cans For The Right Operations
The sliver handling requirements vary from one spinning mill to another (and even within a single mill). To handle such custom demands, leading manufacturers typically have spinning cans of different diameters in their portfolio. Depending on their precise needs, buyers can go for relatively small sliver cans (225 mm), or go for the significantly larger ones (e.g.,1200 mm diameter).
2. Builds Efficiency. Saves Time.
The best spinning cans are made of premium-quality and high-density polyethylene sheets (HDPE sheets). The standardised performance assurance and quality consistency of the cans ensure that they can be handled and used easily – cutting down on operational times and boosting overall efficiency & productivity levels. The versatility of these sliver cans deliver significant competitive advantages to spinning mills.
3. Moving With The Times
Like any other production machinery and equipment, yarn production and sliver treatment procedures are also constantly evolving. To keep pace with the changes, the top spinning can manufacturers – like Jumac Cans – are constantly upgrading their product portfolio with spinning cans and accessories that have enhanced performance, longevity, safety and usability. For these manufacturers, improving constantly is the name of the game.
4. Prompt & Easy Availability
Given the burgeoning demand levels in the textile & yarn sectors, spinning mills can ill-afford extended production downtimes. The easy availability of high-quality HDPE spinning cans is a big relief in this regard. Manufacturers generally have inventories of sliver cans and related accessories – which spinning mill owners can source as and when required, without any problems. No manufacturing delays, no hassles.
5. Role Of Spinning Can Accessories
While spinning cans are, of course, of great value to mills – the importance of key can accessories should never be overlooked. The hardened and durable precision springs (both box and pantograph springs are widely available), the fluff-free caster wheels for easier sliver can mobility, the top & bottom rims and the identification bands – all play extremely important roles in streamlining yarn production and ensuring that sliver quality is not affected in any way.
6. Compatibility With The Latest Spinning Machinery
For synchronised performance, spinning mills need to have a setup where all machines and equipment are compatible with each other. The best spinning cans smoothly fit in as important links in the production chain. These cans are fully compatible with advanced spinning machinery, manufactured by the biggest players (e.g., Truetzschler, Rieter AG, etc.). As a result, the production workflows become smoother and glitch-free.
7. Removal Of All Sliver Imperfections
Spinning cans are extremely important for eliminating the risks of sliver imperfections that generally have adverse impacts on yarn quality. The design of the sliver cans and the smooth surface finishes ensure that there are no sliver damages. In addition, the spinning can accessories (e.g. caster wheels, springs, draw frames, etc.) help in doing away with commonly encountered problems like sliver breakage, sliver stretching, accumulation of dust & fluff, sliver deflections and others.
8. Long Service Life
Leading sliver can manufacturers offer spinning cans that have excellent longevity and service life. Thanks to their robust mechanical strength, there is practically no wear and tear (and hence, no performance loss) in the cans over time. The maintenance requirements of the best spinning cans are minimal as well. Since quality-optimised sliver cans can be used for a long time, mill-owners do not have to lose their sleep over repairs or replacements frequently.
9. Retention Of Sliver Parameters
Most problems in the final yarn quality stem from improper/inefficient sliver handling. Spinning cans manufactured by the top sliver can producers add additional layers of sensitivity and detailing in the process. This helps in the retention of most (if not all) of the original sliver parameters. The doffing cycle is also shortened, boosting productivity & profitability further.
10. Competitive Pricing
In order to deliver maximum value to spinning mills, the top manufacturers make use of state-of-the-art production facilities to design best-in-class sliver cans and accessories. The overall costs of production are effectively managed – and this helps the companies to provide the spinning cans that mills require at affordable rates. The option to buy and use custom HDPE sliver cans without having to incur heavy expenses boosts the usability of the products.
In the increasingly competitive textile & yarn industry, spinning mills have absolutely no room to allow for inefficiencies in their workflows. The importance of using cutting-edge machinery is paramount, the best spinning cans have to be used, and automation has to play a progressively bigger role in the yarn production process. Superior performance and complete quality-assurance are the things that can keep a spinning mill ahead of its competitors, always.
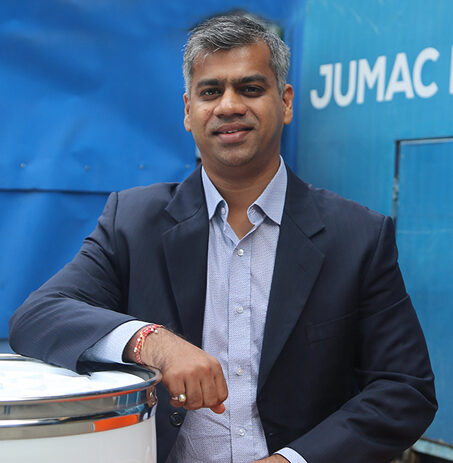
Passionate about transforming the industrial sector of textile and spinning industry with innovative solutions. Director at Jumac Manufacturing, leading spinning cans and accessories manufacturer and exporter from Kolkata, India.