The world might be showing early signs of recovery from…
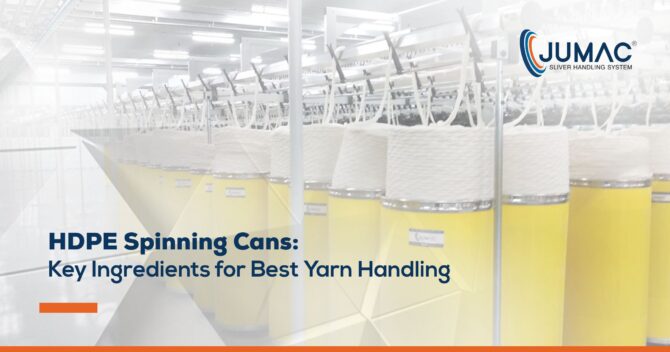
HDPE Spinning Cans:Key Ingredients for Best Yarn Handling
With the world gradually recovering from the Covid-19 pandemic, the demand for yarns has picked up pace – both in India and abroad. Spinning mills are making a conscious attempt to use the best-quality yarns, to deliver buyer-satisfaction and grow their business further. HDPE spinning cans play a vital role in ensuring optimal yarn handling and manufacturing. Let’s take a look at a few factors that make sliver cans important for yarn quality.
Spinning Cans of Different Sizes Are Available
In order to meet the varying buyer requirements, sliver can manufacturers regularly come up with products of different physical characteristics. The diameter of the cans can range from 225 mm to 1200 mm. This allows spinning mills to find and select the can(s) they need. HDPE sliver cans manufactured by the top companies are typically of consistent quality – and they deliver superior performance assurance. Virgin HDPE sheets are used to design the cans. Custom fittings are used – which add value to the different stages of the yarn manufacturing process.
Different types of machinery are used at the facilities of the yarn manufacturing companies. The best sliver cans are designed to be of use in all the key phases of the workflow – like combing, carding, draw framing, and others. As yarn production methods become more and more sophisticated, the design and functionality of the sliver cans also need to be enhanced. That’s the main reason why manufacturers focus on continuous improvement, so that their spinning cans deliver optimal ROI to customers. Companies also generally offer customisations in the sliver cans they provide to clients. All necessary can accessories are made available in a timely manner, so that production workflows are not hampered in any way.
The Role of Sliver Can Accessories
Yarn imperfections are, more often than not, caused by inefficient sliver handling techniques. There are a host of spinning issues that might crop up – if yarn producers do not use HDPE sliver cans with the ‘right’ fittings. Springs (box-type or pantograph) are one of the most important parts of spinning cans. Thanks to the pre-calibrated springs in the cans, load-bearing capacities are boosted, and proper balance is maintained in the cans during operations. The pre-tension of the spinning can spring is kept at minimal levels. The importance of ensuring proper spring load in the sliver cans is immense – and spinning can manufacturers can assist their clients regarding this. Apart from springs, top-class HDPE sliver cans are also fitted with high-strength bottom rim and plate, which enhance the durability and efficiency of sliver can operations. The top manufacturers make sure that the sliver cans are not damaged due to external pressures. The top rim and band of the spinning cans also ensure that the cans do not get cracked/broken during the high-speed rotations. The top/bottom covers do away with probable risks of slipping and can tilting. The onus is on buyers, to ensure that the sliver cans they buy have all the required fittings and accessories.
Best Quality; Competitive Pricing
To keep pace with the rising demand levels, sliver can manufacturers have started to offer an extensive and diversified array of products (cans, fittings, accessories). These ‘smart’ spinning cans ensure that there are no problems in sliver handling – and the entire process remains hassle-free. Since customers are provided detailed technical information about the different types of cans, the usability of these products is enhanced. Expert material handling standards are adopted, to avoid accidental damages and quality losses. The best HDPE sliver can manufacturers have the capacity to ensure high productivity levels, while keeping the average cost of production relatively low. As a result, they can easily offer the best-quality spinning cans to customers at competitive prices. The anti-static sheets used in the sliver cans prevent fibres and/or other external particles from getting stuck in the cans. Hence, common problems like sliver migration and resultant wastage are minimised – and operations can be made more efficient. The ‘environment-friendly’ nature of HDPE cans is another point that warrants a special mention. The cans manufactured by the top companies can be easily recycled and reused, while their maintenance requirements are low. As such, they do not place any additional burdens on the environment.
Caster Wheels of Sliver Cans Make Yarn Handling Smoother
For efficient yarn handling and treatment, proper mobility is very important. Sliver cans are of great help in this regard as well. Leading spinning can manufacturers in India, like Jumac Cans, supply cans with dust/fluff-free caster wheels. The caster wheels, by ensuring safe sliver movements, make the yarn manufacturing process smoother. Spinning mills generally have the option to go for caster wheels in Nylon 6 or polypropylene (depending on their precise requirements). The caster wheels facilitate 360° swivelling – which is important for optimised yarn handling. Risks of yarn damages and/or other imperfections are eradicated. When sourced from a reliable supplier, HDPE sliver cans make sure that there are no caster jamming issues. Identification bands of different types and sizes are supplied by manufacturers. These also play an important role in helping users distinguish between the varied types of sliver cans. Bands of rectangular shapes are also designed. Prior to purchasing, customers should ideally inquire about the detailed specifications of sliver cans. Doing this will remove uncertainties regarding the product features, and help the spinning mills to take more informed purchase decisions. Carefully selected spinning cans ensure superior yarn quality from the start.
HDPE Cans Are The Future
The steadily increasing adoption of HDPE sliver cans for yarn manufacturing clearly underlines the ongoing technological advancements in this sector. The features of the cans are also evolving – expanding their scopes of use. The top-ranked spinning can manufacturers make use of their cutting-edge production facilities to ensure the delivery of best-in-class sliver cans. In order to make things easier for customers, most companies supply the full range of spinning can products and accessories. The combination of skilled manpower resources and state-of-the-art machinery helps top sliver can makers to come up with quality-optimised, performance-assured and easy-to-use products. Companies are also focusing on manufacturing innovative varieties of sliver cans that ensure high lifespan, greater draw frame efficiency, and significantly lower piecing annually. These contribute to further yarn quality improvement. Different varieties of perforated cans are also manufactured by leading suppliers. Bump press cans are yet another new addition in the portfolio of the best spinning can manufacturers. The role of mobile technology in delivering updated information to buyers is becoming increasingly important too. Over the last five years or so, investments in the Indian textile & yarn sector have considerably increased. The production and export figures are rising exponentially. These trends are pulling up the demand for reliable, customized sliver cans as well. As the yarn manufacturing industry continues to grow, we can look forward to even more innovative HDPE sliver cans in future.
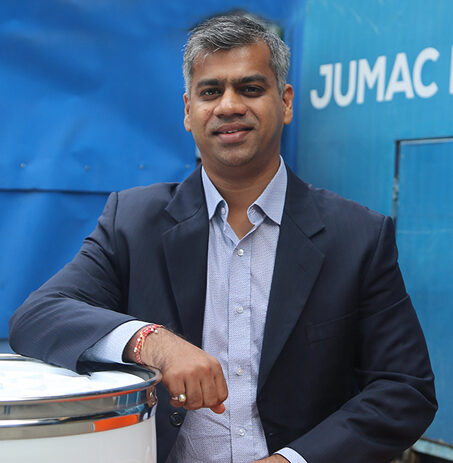
Passionate about transforming the industrial sector of textile and spinning industry with innovative solutions. Director at Jumac Manufacturing, leading spinning cans and accessories manufacturer and exporter from Kolkata, India.