Every indusial sector is facing new challenges as the trends…
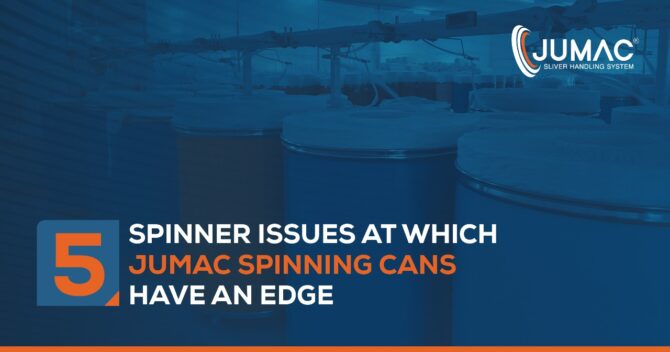
5 Spinner Issues at Which Jumac Spinning Cans Have an Edge
While the worldwide textile market is growing at a rapid clip, the quality of yarn remains a point of concern among buyers. Usage of sub-optimal spinning cans, along with poor sliver handling techniques, are among the biggest reasons behind such problems. From sliver stretching, deflections and breakage, to caster jamming and dust/fluff accumulation – yarn spinner issues can be many and varied. This is where the operations of Jumac Cans make a difference. With its state-of-the-art HDPE spinning can manufacturing standards and regular quality checks – the company ensures world-class sliver handling solutions. Over here, we take a look at some yarn spinning issues that Jumac does away with:
Avoiding Sliver Deflection Hassles
One of the most common sliver handling issues is sliver deflection. This problem can hamper the yarn manufacturing process and affect yarn uniformity. In order to avoid such sliver deflections, the Jumac spinning cans come with tough and highly reliable springs. The springs in the spinning cans make sure that the distance between the lifting roller and the top portion of the sliver coils remains the same at all times. As a result, the can rim and the plate remain close when the can is empty – and there are no sliver deflections. Due care is given to maintain the sliver column height, the lifting roll, and the other key components of sliver can operations. Depending on the type of the spinning cans, pantograph springs or box springs are used. These help in maintaining proper balance, and rules out tilting risks. Molded polypropylene is used to design the bottom of the spring. These ensure that the spinning cans are not damaged in any way when the spring is being inserted or removed. The springs are maintained carefully, and mechanical fatigue is minimised – so that the spring stiffness remains optimal.
Jumac Spinning Cans Minimise Sliver Stretching
Sliver stretching is another frequent problem that diminishes the performance/productivity of HDPE spinning cans. This issue crops up when the sliver gets excessively stretched by its own weight. As a result, the overall yarn spinning standards go down. To counter this problem, the springs used in the Jumac spinning cans prove to be extremely effective. The shape of the cans is maintained by the plate and the bottom rim. Particularly when the spinning cans are rotating fast, these ensure minimal sliver stretching and/or collapses. At Jumac, each HDPE spinning can is designed and fitted with stable and consistent components – which bolster overall sliver quality and yarn quality. The company follows an agile, process-driven operational approach, to ensure glitch-free spinning can performance. The Jumac spinning cans are constantly upgraded, with a focus on constant improvement and adherence to international quality standards. In particular, the sliver withdrawal process is standardised – ruling out chances of sliver stretching.
Doing Away With Sliver Breakage Risks
Spinning cans typically have to be handled in a smooth and efficient manner. Unfortunately, this is not done in many cases – leading to sliver breakages, yarn inconsistencies and overall quality degradation. The keen eye for detail that the in-house staff at Jumac Cans has makes sure that such problems never occur. All relevant process parameters and mechanical properties are considered carefully – and spinning cans of different sizes/diameters are manufactured accordingly. The cans are designed in a manner that ensures that the lifting roller and sliver column top layer remain close (the movement of the sliver column is carefully managed). Detailed testing is done to detect and resolve risks of stiffness-loss in the spinning can springs. The spring pressure gradually goes down, as the volume of the sliver decreases. The can plate that contains the sliver moves up – and there is an expansion in the bottom part of the spring. By making this process smooth and seamless, Jumac makes sliver breakage risks practically nil.
Usage of Draw Frames to Prevent Sliver Accumulation
The way in which the rotor of the HDPE spinning cans groove has a lot to do with determining the yarn quality. Accumulation of dust and fluff (sliver accumulation) can affect this operation – causing yarn quality to deteriorate. Jumac handles this risk by using efficiently designed draw frames with powerful suction tools. More than 85% of the total sliver accumulation can be quickly removed by the draw frames. As a result, the efficiency of the spinning cans do not go down over time. The grip of the HDPE cans on the sliver (particularly important for fine sliver) is maintained at the proper level. This helps in removing irregularities in the blended sliver. The sliver drafting process also becomes more efficient. Apart from removing accumulated dust and fluff, the draw frames in the spinning cans ensure that the collected waste can be easily recycled and reused. Performance optimisation of the Jumac spinning cans ensure maximum productivity and cost-effectiveness.
Caster Jamming Problems Are Not Present
Sliver cans are often used to move sliver across the different sections of manufacturing plants. If the caster wheels in the cans get jammed in any way, the movement becomes problematic – and there is every likelihood of the sliver getting damaged. To stay away from such glitches, Jumac makes use of high-mobility caster wheels in its HDPE spinning cans. These caster wheels are generally custom-fitted – depending on the size and type of the cans. Enhanced movement efficiency is the biggest advantage of the caster wheels used in the Jumac cans. In addition, the wheels also play an important role in making sure that there are no chances of the loaded sliver cans getting tipped over. The caster wheels are non-abrasive, and have excellent tensile strength and tear strength properties. The spinning cans are generally used under high temperatures – and Jumac makes sure that the caster wheels do not undergo size and/or shape damages, when subjected to such extreme conditions. Nylon 6 and polypropylene are generally used as the material of caster wheels.
Sliver handling and optimised usage of spinning cans go a long way in enhancing and maintaining yarn quality standards. Jumac cans – with its expert business operations and 360° in-house monitoring – ensures that all probable sliver problems are kept at an arm’s length. The rising demand for premium-grade yarns is pulling up the need for efficient, seamlessly designed HDPE spinning cans, and Jumac is steadily consolidating its position as a market leader in this regard.
Recommended Reading: How to choose the right HDPE Spinning Can for your Spinning Mill
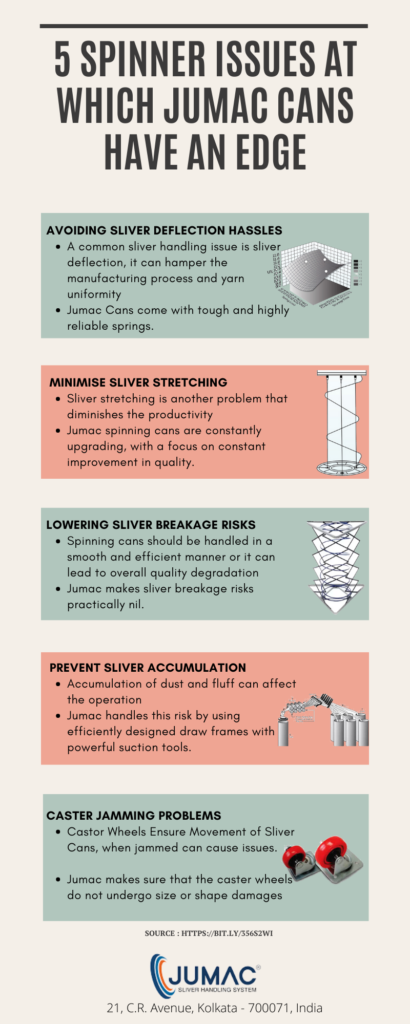
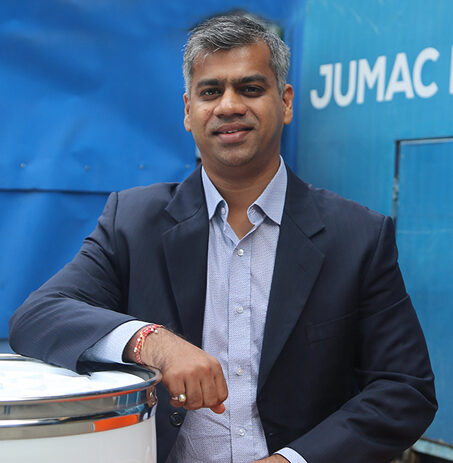
Passionate about transforming the industrial sector of textile and spinning industry with innovative solutions. Director at Jumac Manufacturing, leading spinning cans and accessories manufacturer and exporter from Kolkata, India.