Handling sliver cans with care and consciousness For Spinning Industry,…
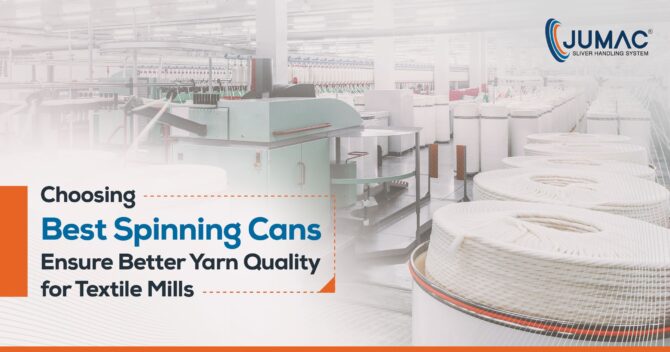
Choosing Best Spinning Cans Ensure Better Yarn Quality for Textile Mills
The demand for world-class and fully customised spinning cans is growing fast across the world. Given the crucial role these sliver cans play in optimizing yarn quality, this trend is hardly surprising. Automation and technological innovation are changing the face of the Indian textile industry – bolstering productivity and efficiency levels, and improving ROI figures. The various competitive advantages of this sector, together with the growing production opportunities, are driving the spinning cans industry (and, of course, the worldwide fibre market) forward. In here, we will highlight how the best spinning cans ensure better yarn quality for textile mills:
HDPE Spinning Cans Deliver Enhanced Versatility
The products supplied by different spinning can manufacturers tend to vary in quality and durability. It is extremely important for textile mills to find and select HDPE (high-density polyethylene) spinning cans that would help in improving yarn quality. Sliver cans of sub-par quality tend to get damaged during the various spinning stages – causing neps and other imperfections. Since the best spinning cans make sure that the original parameters of sliver are maintained, there are no uncertainties over the output quality. The versatility of the spinning cans is a huge advantage. For practically all types of fibers and yarn volumes – right from synthetic yarns and cotton, to blended yarns – spinning cans can be used in different scenarios. Installation and combination of the cans are done as per precise requirements. Good spinning cans ensure high levels of consistency in sliver formation. Right through the yarn production stages, sliver regularity is maintained, and hairiness (if any) is removed. In order to ensure that there is no tilting or any other such problems, many spinning cans are anti-static, and are fitted with pantograph/box springs. The top manufacturers and suppliers of sliver cans focus on providing scratch-resistant and corrosion-resistant spinning cans that are lightweight as well. Excellent dimensional accuracy, ergonomic efficiency, and suitable spring tension are some of the other characteristics of the best spinning cans.
Spinning Cans Deliver A Fine Combination of Yarn Quality and Productivity
In order to sustain and be successful in the highly competitive global market, textile mills need to produce yarns of the best possible quality. Productivity is an equally important factor – since that determines whether a mill’s supply can actually match the demand levels. Spinning cans deliver the best results in this regard. With high-quality sliver cans, it becomes easy to optimize the quality of yarns – without compromising on the productivity and time-to-market metrics. Ring spinning is generally considered to be the most suitable spinning method. By correctly setting up and using HDPE spinning cans, the textile mills can produce yarns of high structural strength and softer texture. The speed of the drawing operations can also be managed easily, ensuring uniform quality. A common problem with poor-quality yarns is their tendency to break at the time of spinning. Sliver cans rule out such risks. In addition, handling these spinning cans is simple enough – while the maintenance costs are not high either. Therefore, the textile mills can keep their costs of production low. As and when required, parts of the spinning cans can be repaired/replaced without any hassles. This adds to the usability factor of the cans further. Good spinning cans typically ensure that the yarn has excellent dyeing properties, colour integrity and moisture-absorption features.
Coated Springs and Seamless Caster Movements Of The Spinning Cans Play An Important Role
In order to ensure that there is no rusting and/or excessive roughness, manufacturers generally use galvanised or stainless steel to design the spinning cans. Apart from the enhanced durability, the stainless/galvanised steel spinning cans make sure there is no sliver accumulation whatsoever. While purchasing spinning cans, textile mills have to check the coated springs of these cans. Serving as one of the most important components of sliver cans, these coated springs rule out imbalances and other unforeseen jerks/movements during the operational process. Reputed manufacturers design HDPE spinning cans with swiveling casters that facilitate 360° movement. Since there are no glitches in the caster movement, it becomes easier to maintain uniformity in yarn quality. The sliver is held in place by the top plate of the spinning cans. Due care is also taken in selecting the HDPE sheets for the sliver cans. The best HDPE sheets are scratch-resistant, and they do not cause any overlapping-related problems. Ideally, textile mills should go for HDPE cans with standard kicking bands. Generally, the sheets are assembled onsite. The top-edge of the spinning cans have seamless evenness with pre-specified maximum deviations. The cans have impact-resistance, along with powerful uprightness. In order to ensure that the sliver grip is steady, radial/circular embossed sheets are used in the spinning cans.
With Technological Advancements, Spinning Cans Are Evolving
By the end of 2027, the value of the worldwide spinning machines market will zoom to just a shade under $7.5 billion. Constant innovation and implementation of automation will continue to power the growth of this sector. Since spinning cans have the ability to effectively use recycled fiber, textile wastes are minimal – and there are no extra environmental burdens. While the Covid-19 pandemic did slow down operations in the textile sector – this industry is already showing signs of strong recovery. Sliver cans keep the fibers compact, prevent end-breakage, and add greater efficiency to the yarn-making process. Since the yarn length is utilised in the best possible manner, the quality of the yarn is optimised. There are practically no speed variations or slippage risks. In comparison with manual yarn handling, spinning cans help in the production of yarns that are stronger, have better elongation, and have minimal hairiness/other imperfections. The absence of any disturbance in the fiber orientation also plays an important role in avoiding yarn-quality deterioration. By using quality-assured sliver cans, the binding of the fibers at the edge can be improved. There is better fiber cohesion as well. HDPE cans are typically tough, with high service life and easy maintenance. As such, they deliver excellent value-for-money for textile mills. For high-precision yarn-making, the importance of spinning cans is immense.
Quality Spinning Cans Ensure Quality Yarns
For the top spinning can manufacturers, continuous improvement is the name of the game. Right from HDPE sliver cans to the accompanying springs and casters – everything is quality-tested and supplied to the textile mills, as per the latter’s requirements. Thanks to the focus on innovation, these manufacturers are being able to design more powerful and customised spinning cans at competitive cost levels. As a result, the textile mills are finding it easy enough to get best-in-class sliver cans at affordable rates. All the requisite technical information and details about the spinning cans are provided so that users do not face any difficulty during the yarn-making process. The finest sliver cans have bottom and top covers made from moulded plastic – which boosts durability. The virgin HDPE sheets used have fine finishes and ensure ease of handling. Premium-grade spinning cans are instrumental in bolstering the sliver loading capacity of the system, along with increasing the overall operational efficiency. Therefore, yarn production becomes quicker and more quality-oriented. Operational time goes down as well, and there are no material handling issues. With advancements in spinning can design and manufacturing, the yarn-making process is undergoing constant improvement. The focus is always on optimising the product quality as well as on ramping up production volumes. Spinning cans work as vital cogs in the overall process – and they will become even more efficient in the foreseeable future.
Spinning Cans Add Flexibility and Offer Economic Advantages
The quality of yarns depend crucially on the flexibility and adaptability of the manufacturing process. This is where the value of good spinning cans come into the picture. Leading sliver can manufacturers, like Jumac Cans, design cans that are used to spin different types of yarns. The best spinning cans ensure a blend of yarn-making flexibility and diversity. This, in turn, enables the textile mills to supply yarns that meet the precise requirements and preferences of customers. Switching from compact yarn to ring yarn is easy too. Usage of spinning cans manufactured by a reputed supplier yields significant economic benefits as well. The cost efficiency can go up considerably, while energy-savings are also boosted. Since the total energy consumption is low – and innovative, custom components are made use of – superior-quality yarn can be produced. The compact designs of the HDPE spinning cans ensure that they can be set up and operated in relatively small spaces. Raw-materials are optimally utilised, to minimise wastes and maximise output quantity as well as quality. Textile mills can enhance their production volumes and ensure product excellence. Spinning cans are generally interoperable with other operating machinery. There are minimal stress damages in these cans over time – and the rotor-spinning capabilities are top-notch. Since good spinning cans are malleable and easily foldable, transporting them from one place to another is also hassle-free.
Recommended Reading: Jumac Spinning Cans Ensure Optimal Compatibility with Multi-Brand Spinning Machines
With more and more spinning can manufacturers embracing the latest production technologies, the global market for spinning cans is all set to grow exponentially over the next few years. Across the world, the demand for high-quality yarns is rising – and that, in turn, is pulling up the sales and export figures of premium-grade sliver cans. By selecting the best spinning cans, textile mills can go a long way in ensuring that their yarns are of the highest quality.
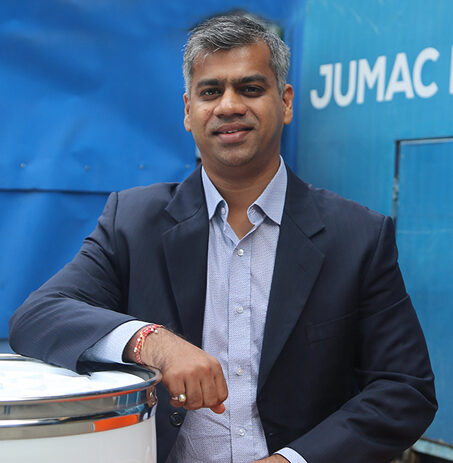
Passionate about transforming the industrial sector of textile and spinning industry with innovative solutions. Director at Jumac Manufacturing, leading spinning cans and accessories manufacturer and exporter from Kolkata, India.