Although every spinning unit aims towards producing 100% uniform yarn,…
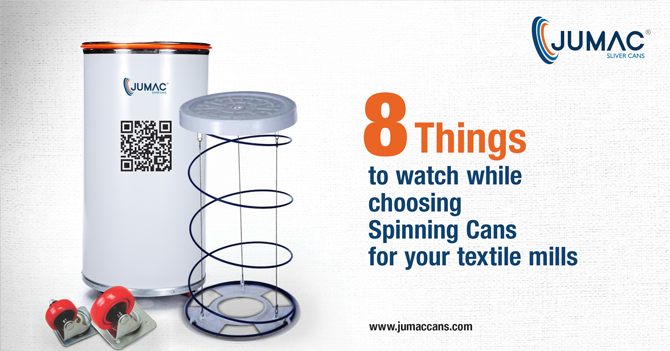
8 Things to Watch While Choosing Spinning Cans for Your Textile Mills
Clothing has always been an essential requisite for humanity. Emerging fashion trends act as a boon to the textile industry to create more quality products with innovative solutions. The spinning industry’s prominent role is to produce quality yarn by converting cotton fibre to yarn. Any spinning mills prime obligation is to produce 100 per cent uniform yarn. Today spinners are taking the initiative with their upmost effort to increase productivity with improved yarn quality and to increase the economic competence in the spinning mill. There are several stages involved in this process, like carding, drawing, combing, spinning, weaving etc. At each stage, while transforming raw fibre to yarn, it is liable to imperfections. Even a small amount of furriness in the sliver (raw material of yarn) at any phase of the spinning processes will affect the yarn’s overall quality. Therefore, to retain the sliver properties and for good sliver handling spinning cans are needed. This is where spinning cans become prominent in attaining the elite quality of uniform or even yarn.
Inevitabilities of spinning cans
Spinning cans are cylindrical shape packaging containers used in every phase of the spinning process. It used to store and transport materials from one stage to another to subsequent machines. Cans are essential to provide high degree protection for smooth handling of the processed fibre during transportation. These spinning cans are available at various sizes to match up with the machine parameters and process parameters. This will reduce the yarn breakage or nil the sliver’s hairiness by maintaining its roundness and shape throughout its lifetime. Spinning cans with its seamless and smooth surface adds sensitivity to sliver handling system by avoiding any possible damage during the spinning process. These are produced with high strength ratio to withstand the machines’ pressure during operation and transportation of sliver. Manufactures like Jumac Cans strive to create strong spinning cans with sturdy features to hold on to any effects and save yarn from damages. Finest materials are put to use to produce these cans for ensuring long durability and viability to investment. Spinning mills follow excellent sliver handling methods to retain sliver properties in turn best quality of yarn.
Deciding the right spinning can
Choosing the right spinning Can for your textile mill is an essential aspect of producing high-quality yarns by retaining sliver properties. Selecting an inappropriate fit could be a hindrance for the spinning process rather than a benefit. Textile mills are modernized with well- equipped hi-tech spinning machinery and technology to adhere to global standards. Spinning cans are purposely designed and modified with innovations to tend to the demands of modern textile mills.
There are eight basic features to be considered before making a choice.
Body sheet
Spinning cans body sheet are made up of high-density polyethene sheets. These cans are easily prone to wear and tear as they are the cans’ most exposed parts. Spinners preferably choose for virgin quality HDPE spinning cans with seamless cylindrical body. They also look for smooth anti-static finish and standard thickness on the inner surface. The HDPE body sheet is the preferred choice to ensure cylindrical integrity and a perfect butt weld with good flexibility.
Sizes
Every type of spinning mills, both small and large, requires hundreds of cans to store, collect and different forms of sliver. Spinning cans are available at various sizes, with accessories in the market from small (225mm) to extra-large size (1200mm). Textile mills mostly prefer HDPE spinning cans of standard size and reliable quality. Manufactures of sliver cans even produce customized cans to adhere to the demands of the customers.
Machine compatibility
The modern spinning mills are equipping themselves with several types of high technology spinning machines. The sliver cans must be selected considering the machines’ compatibility for all stages in the spinning process like carding, combing, draw frame, roving and rotor spinning. Aluminium sliver cans are suitable for jute textile mills, and HDPE sliver cans are commonly used in textile mills. Cans are produced with sturdy nature comprising high strength and agility to minimize wear and tear and retain uniform sliver by producing elite quality yarn.
Top and Bottom Covers
Top and bottom covers are an added advantage to sliver cans prevent it from slipping from their bases. In spinning operation, a massive amount of centrifugal force tends to disturb the cans’ physical shape, may cause the cans to tilt or slip from their positions. Plastic top covers are used for 9 inches to 24-inch cans and galvanized steel sheets are used for cans size up to 48 inches. Top covers are used with an anti-slippage surface to give a good grip. Plastic bottom covers provide additional capacity for storage.
Top Rims and Bands
Top Rims and Bands made up of stainless steel or galvanized steel with a smooth finish. They hold the shape of the cans firmly from cracking and collapsing when machines rotate at high speed. Therefore, it prevents the rusting of rough edges wherein sliver will accumulate and from collapsing the sliver structure can.
Bottom Rims and Plates
Bottom Rims and Plates are made of galvanized iron by heavy-duty power press. They are presented with unique ribs and contours to hold the shape and give more generous support to the sliver cans. The bottom plates will increase the cans’ longevity and allow perfect adjustment to the toothed belts.
Springs
Springs are used to ensuring the distance between the feed roller and the top layer of sliver to be stable. Anti-rust springs are specially heat-treated and calibrated for acquiring the required sliver weight. Box springs are heat treated springs made of high carbon steel wire to enable uniform load and movement during operations. These are suitable for smaller diameter cans or for over centre coiling mechanism. Pantograph springs are electro-welded galvanized shutters in criss-cross shape to ensure constant spring movement and maintain uniform sliver height. Springs are hardened and tempered with care to retain the original sliver properties and preferred a wide range of diameter of cans. Spring Bottoms are made of moulded polypropylene. It is used to hold them firmly and does not harm the can while inserting or removing the spring.
Caster Wheels
The caster wheels are made up of high pressed zinc coated body with polypropylene and nylon 6. These must possess high tensile strength, abrasion resistance and heat stability for longer life of the product. The casters are positioned under bottom plates with 360-degree rotation wheels to ease the cans’ transportation during different production stages. Swivel castors are preferred over the rigid type of castors for feasibility in the spinning mills. To attain the longer life of the caster wheels, make sure that they never get easily entangled with corrosive chemicals or dirt utilized for yarn production.
Spinning mills are always looking for solutions to improve their flexibility, adaptability spinning speed, and consistency in producing even yarn. Spinning cans continue to be a significant part of any textile mills in efficiency and effectiveness. In textile mills, unexpected sudden breakdown or imperfection can occur at any stage of the operation and are likely to incur severe spinners’ losses. Spinning cans manufactures a wide variety of spinning cans, both standard and customized sizes with identification bands to ensure that the spinning units can obtain optimum performance.
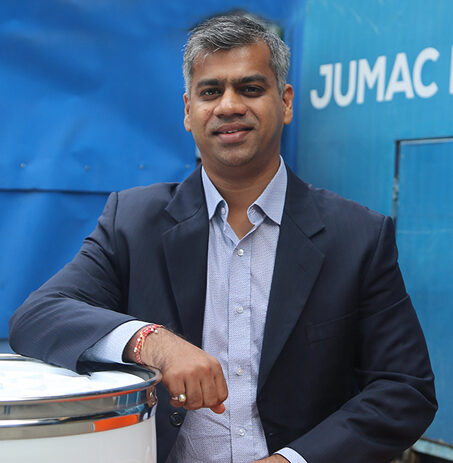
Passionate about transforming the industrial sector of textile and spinning industry with innovative solutions. Director at Jumac Manufacturing, leading spinning cans and accessories manufacturer and exporter from Kolkata, India.