Often referred to as the ‘heart of the spinning process’,…
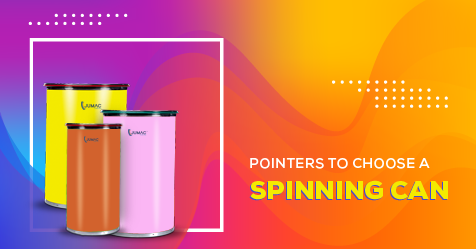
6 Important Points to Look for Before Choosing a Spinning Can
Choosing the right Spinning Can is key to produce the best quality of Sliver in a Spinning Mill. A good Spinning Can not only delivers a quality product but also lasts for a longer time giving economic viability to the investment. Here are 6 important points you should look for:
Premium Quality HDPE Sheet for a Kicking Bend.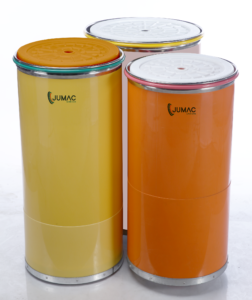
Never compromise on the Body Sheet as it is the most exposed part of the Spinning Can for regular wear and tear. Always go for HDPE Sheets with Kicking Bend with Standard Thickness, Zero Scratch Damage, Zero Ovality, Zero Overlapping, and Seamless press at Joint. The sheets should be systematically assembled at the site. Also, look for Anti-Static finish in the inner surface of the sheet.
Stainless Steel for Top Rim & Band
We suggest using Stainless Steel for Top rim & binder to prevent rusting and rough edges wherein sliver can accumulate & impact its quality. Galvanized Bottom Rim and Plate in all types of Cans. Use steel rivets at 7-8 inch interval to ensure no gap between spares and the body sheet to avoid fiber accumulation. Use Embossed Sheets for Bottom Rims and Plates.
Smooth 360-Degree Castor Movement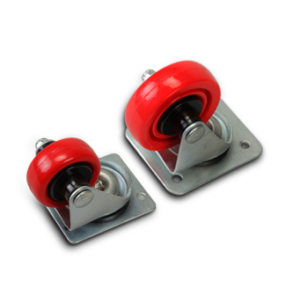
Look for Ball Bearing Type 360-Degree Swiveling Castors, directly fixed to the bottom plate using nut bolts. Ensure no play in the castor movement and minimum gap from the floor.
Use Stainless Steel Wire with Plastic Coating in Tying Chord
Use Non-Adjustable Stainless Steel wire with Plastic Coating in Tying Chord, while binding the springs with the Bottom Plate. Keep equidistance between three parallel chords. Do not directly tie with the top plate.
Springs are the Heart of the Can 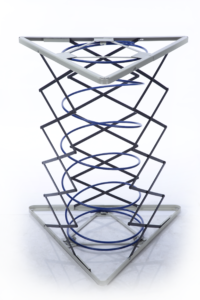
Use coated springs for your can and check the Spring Thrust as per specifications to avoid ununiformed movement and balance during operations. Proper Specification with pretension value must be filled in the specification sheet while asking from the supplier.
Choose the Perfect Top Plate to hold the Sliver well
Top Plate should be produced in a single die. Use plastic sheets for up to 24-inch Cans and 18G Steel Sheets for up to 48-inch Cans. Use Embossed Sheet (Radial Lines, Circular Lines and Pyramid Points) for better grip on the spring and uniform holding of sliver.
You should also ensure Evenness of the Top-Edge with a maximum deviation of 4.5 mm, Uniform circularity of the Can with a tolerance of 10mm, Uprightness of the can with a max deviation of 10mm and make sure that the Cylinder and Joints are impact resistant.
Keep the above 6 points in mind while choosing Sliver Cans for your Spinning Mill.
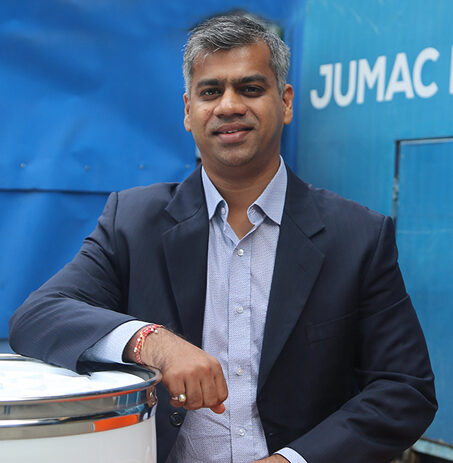
Passionate about transforming the industrial sector of textile and spinning industry with innovative solutions. Director at Jumac Manufacturing, leading spinning cans and accessories manufacturer and exporter from Kolkata, India.